TM-650
IPC-TM-650:試験方法(テストメソッドマニュアル)
試験方法概要
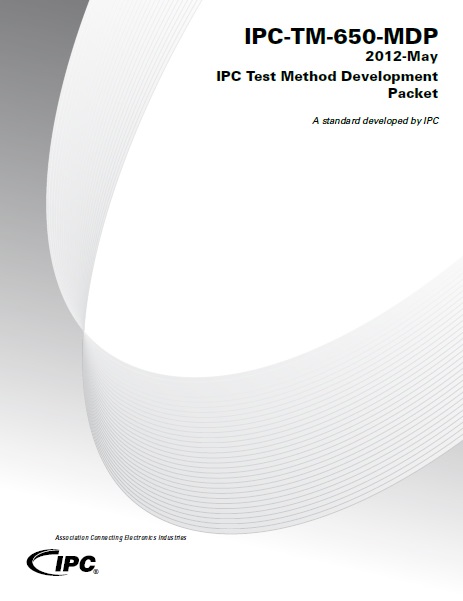
本マニュアルは、基本的な環境、物理的、電気的試験を含む、電子および電気部品試験における統一的な方法を設けたものです。統一化された試験方法については、各関連標準規格のタスクフォースが中心となり開発・改善を行っています。
※一部重要な試験方法については、日本語訳があります。(参考訳:無料ダウンロード可)
※TM-650インデックスはこちら
マニュアルの目的
これらの試験方法は、IPC規格および仕様への準拠を目的として開発されました。本マニュアル内に記載されている試験は、単一の地理的立地における実際のサービス業務の、厳密かつ確実な説明として解釈されるものではありません。周知の通り、その時々に行われる実際のサービス試験こそ、具体的な立地における唯一真の業務試験になりうるのです。任意の試験方法に関する厳密な試験条件とは、ラボで得られた、再現可能な結果を指します。
合否判定
試験方法には、合格/失敗の基準が一切含まれていません。これらの情報は、各試験方法を参照する個別の仕様や規格に記されています。
各セクション紹介
セクション 1.0 – レポートと測定の分析法
セクション 2.1 – 目視試験の方法
セクション 2.2 – 寸法検査法
セクション 2.3 – 化学試験法
セクション 2.4 – メカニカル試験法
セクション 2.5 – 電気的試験法
セクション 2.6 – 環境試験法
日本語版の提供について
お客様から多数のご要望を頂き、一部の試験方法につきまして、参考として日本語翻訳を行いました。本翻訳版は無料でダウンロードして頂くことが可能です。ただし、参考役としての提供になりますので、使用に関しましては、原文を必ず確認し、使用者様の責任の上、ご利用ください。尚、今後も参考訳を行った試験方法は下記に更新していきます。追加分の入手をご希望の方は、お手数ですが再度、導入事例ダウンロードよりお申し込みください。
※2.3.x-2.5.7.1,2.6.7.1など 計10本の日本語版追加(2021/10)
※2.6.x 環境試験法にて10本の日本語版追加(2022/03) 計20本の日本語訳有
※2.3.25.1、2.3.32D、2.4.14.2A、2.6.15Cの日本語版を新たに追加(2023/06)、2.6.25の最新C版の日本語訳を更新
セクション 1.0 – レポートと測定の分析法 | |
---|---|
TM 1.1C | 初めに – 1/03 |
TM 1.2A | 校正 – 1/03 |
TM 1.3A | 環境条件 – 1/03 |
TM 1.4A | レポート、全般 – 1/03 |
TM 1.5A | レポート、形式 – 1/03 |
TM 1.6A | 数値レポート – 1/03 |
TM 1.7A | レポート、無効な試験結果 – 1/03 |
TM 1.8A | バイナリデータ向け測定精度の推定 – 1/03 (計算機とユーザーガイド含む) |
TM 1.9A | 変数データ向け測定精度の推定 – 1/03 (計算機とユーザーガイド含む) |
セクション 2.1 – 目視試験の方法 | |
---|---|
TM 2.1.1E | マイクロセクショニング、手動 – 5/04 |
TM 2.1.1.1 | マイクロセクショニング、 セラミック基板 – 12/87 |
TM 2.1.1.2A | マイクロセクショニング?半自動式または自動式技術マイクロセクショニング装置 (オルタネート) – 5/04 |
TM 2.1.2A | ピンホール評価、染料浸透法 – 3/76 |
TM 2.1.3A | メッキ – スルーホール 構造評価 – 8/76 |
TM 2.1.5A | 表面試験、アンクラッドとメタルクラッド材 – 12/82 |
TM 2.1.6B | ガラス繊維の厚み – 12/94 |
TM 2.1.6.1 | 繊維補強の重量 – 12/94 (2.3.12より番号を再割り当て) |
TM 2.1.7C | ガラス繊維のスレッドカウント – 12/94 |
TM 2.1.7.1 | スレッドカウント、有機繊維 – 12/87 |
TM 2.1.8B | 仕上がり – 12/94 |
TM 2.1.9 | 表面引っかき傷試験 メタルクラッドフォイル – 5/86 |
TM 2.1.10A | 不溶解ジシアンジアミドの目視検査 – 12/94 |
TM 2.1.13B | フレキシブルプリント基板材のボイド検査 – 5/12 |
セクション 2.2 – 寸法検査法 | |
---|---|
TM 2.2.1A | メカニカル寸法検証 – 8/97 |
TM 2.2.2B | オプティカル寸法検証 – 8/97 |
TM 2.2.4C | 寸法安定性、フレキシブル誘導体材料 – 5/98 |
TM 2.2.5A | マイクロセクショニングを利用した寸法検査 – 8/97 |
TM 2.2.6A | 穴寸法測定、ドリル穴 – 8/97 |
TM 2.2.7A | 穴寸法測定、メッキ – 5/86 |
TM 2.2.8 | 穴位置 – 4/73 |
TM 2.2.10A | 穴位置と 導体位置 – 12/83 |
TM 2.2.12A | 同厚み、重量別 – 3/76 |
TM 2.2.12.1 | 処置済・未処置銅はくの全厚と形状要素 – 9/87 |
TM 2.2.12.2 | 開放可能キャリアつき銅はくの重量と厚み – 7/89 |
TM 2.2.12.3 | エッチング可能キャリアつき銅はくの重量と厚み測定 – 7/89 |
TM 2.2.13.1A | 厚み、穴のメッキ処理、マイクロオーム法 – 1/83 |
TM 2.2.14 | はんだ粉末粒度分布 – タイプ1?4向け選別法 – 1/95 |
TM 2.2.14.1 | はんだ粉末粒度分布 – 測定顕微鏡法 – 1/95 |
TM 2.2.14.2 | はんだ粉末粒度分布 – 光学画像解析法 – 1/95 |
TM 2.2.14.3 | 最大はんだ粉末粒度の測定 – 1/95 |
TM 2.2.15 | ケーブル寸法 (フラットケーブル) – 6/79 |
TM 2.2.16 | 穴空きパネルを利用したアートワークマスタ評価 – 12/87 |
TM 2.2.16.1 | オーバーレイによるアートワークマスタ評価 – 12/87 |
TM 2.2.17A | 金属ファイルの表面あらさと形状 (接触スタイラス法) – 2/01 |
TM 2.2.18 | 機械測定によるラミネート厚の決定 – 12/94 |
TM 2.2.18.1 | メタルクラッドラミネート厚の決定、断面 – 12/94 |
TM 2.2.19 | 孔パターン位置の測定 – 12/87 |
TM 2.2.19.1 | ラミネートとプリプレグパネルの長さ、幅、直角度 – 12/94 |
TM 2.2.20 | はんだペースト金属含有量、重量別 – 1/95 |
TM 2.2.21 | 高密度相互接続(HDI)/マイクロビア技術における誘電体の平面性 – 11/98 |
セクション 2.3 – 化学試験法 | |
---|---|
TM 2.3.1 | 化学処理、適切な加工材 – 4/73 |
TM 2.3.1.1B | メタルクラッドラミネートの化学洗浄 – 5/86 |
TM 2.3.2G | フレキシブルプリント基板材の耐薬品性 – 12/07 |
TM 2.3.3A | 絶縁材料の耐薬品性 – 2/78 |
TM 2.3.4B | 耐薬品性、マーキング塗料とインキ – 8/87 |
TM 2.3.4.2A | 溶剤曝露によるラミネート、プリプレグ、被覆フォイル製品の耐薬品性 – 12/94 |
TM 2.3.4.3 | コア材料の塩化メチレンに対する耐薬品性 – 5/86 |
TM 2.3.6A | 過硫酸アンモニウムによるエッチング法 – 7/75 |
TM 2.3.7A | エッチング、塩化第二鉄法 – 7/75 |
TM 2.3.7.1A | 塩化第二銅によるエッチング法 – 12/94 |
TM 2.3.7.2A | アルカリエッチング法 – 12/94 |
TM 2.3.8A | 引火性、フレキシブル絶縁材料 – 12/82 |
TM 2.3.8.1 | フレキシブルプリント配線の引火性 – 12/88 |
TM 2.3.9D | プリプレグと薄積層の引火性 – 8/97 |
TM 2.3.10B | ラミネートの引火性 – 12/94 |
TM 2.3.10.1 | プリント配線ラミネートのソルダマスクの引火性 – 8/98 |
TM 2.3.11 | ガラス繊維構造 – 4/73 |
TM 2.3.13A | 液体はんだ付け用フラックスの酸化測定- 電位差滴定と目視滴定法 – 6/04 |
TM 2.3.14 | プリント、エッチング、プレート試験 – 4/73 |
TM 2.3.15D | 銅はくまたはメッキの純度 – 5/04 |
TM 2.3.16B | プリプレグの樹脂含有量、焼失減量別 – 12/94 |
TM 2.3.16.1C | プリプレグの樹脂含有量、処理済重量別 – 12/94 |
TM 2.3.16.2 | プリプレグの処理済重量 – 12/94 |
TM 2.3.17D | プリプレグの樹脂流動率 – 8/97 |
TM 2.3.17.2B | 無流動プリプレグの樹脂流動 – 8/97 |
TM 2.3.18A | プリプレグ材料のゲル化時間 – 4/86 |
TM 2.3.19C | プリプレグの揮発性成分含有量 – 12/94 |
TM 2.3.21 | ハルセル法のメッキ品質 – 8/97 |
TM 2.3.22 | 銅保護膜の塗布品質 – 2/78 |
TM 2.3.23B | 加硫 (恒久性) 熱加硫ソルダマスク – 2/88 |
TM 2.3.23.1A | 加硫 (恒久性) 紫外線主導ドライフィルムソルダマスク – 2/88 |
TM 2.3.24 | 金メッキの多孔性 – 2/78 |
TM 2.3.24.1 | ニッケルめっき銅基板に電気めっきされた、金の有孔度試験 電子写真方式 – 10/85 |
TM 2.3.24.2A | 銅基合金とニッケルの金属被覆の多孔性(硝酸蒸気試験) – 8/97 |
TM 2.3.25D | 溶媒抽出剤の固有抵抗による、イオン性表面汚染の検出と測定(ROSE) – 11/12 |
TM 2.3.25.1
![]() |
ベア・プリント配線基板のイオン性洗浄度試験 – 10/00 |
TM 2.3.27 | 洗浄度試験 – 残留ロジン – 1/95 |
TM 2.3.27.1 | ロジンフラックス残留分析-HPLC 法 – 1/95 |
TM 2.3.28B
![]() |
回路基板のイオン分析 イオンクロマトグラフィーによる分析方法 – 11/12 |
TM 2.3.28.1 | はんだ付け用フラックスとペーストのハロゲン化物含有量 – 6/04 |
TM 2.3.28.2 | イオンクロマトグラフィーによるベア・プリント基板洗浄度の分析 – 12/09 |
TM 2.3.29 | 引火性 フレキシブルフラットケーブル – 11/88 |
TM 2.3.30A | 無水フッ化炭素溶剤の溶剤 pH 測定 – 11/81 |
TM 2.3.31 | UVキュアリング可能材のキュア度合い – 2/88 (確認済) |
TM 2.3.32D
![]() |
フラックス誘導による腐食 (銅鏡法) – 6/04 |
TM 2.3.33D | フラックスにおけるハロゲン化物の存在 クロム酸銀法 – 6/04 |
TM 2.3.34C | 固形含有量 フラックス – 6/04 |
TM 2.3.34.1B | フラックス塗布またはフラックス入りはんだにおけるフラックス率 – 1/95 |
TM 2.3.35C
![]() |
ハロゲン化物含有量 – 定量的 (塩化物と臭化物) – 6/04 |
TM 2.3.35.1A | スポットチェックによるフッ化物 フラックス – 定性 – 6/04 |
TM 2.3.35.2A | フッ化物濃度 フラックス – 定量 – 6/04 |
TM 2.3.36 | 塩素系溶剤の酸受入れ度 – 10/85 |
TM 2.3.37B | 接着剤塗布誘導体膜の揮発性成分 – 5/98 |
TM 2.3.38C | 表面有機不純物の検出試験 – 5/04 |
TM 2.3.39C
![]() |
表面有機不純物の識別試験 (赤外線分析法) – 5/04 |
TM 2.3.40 | 熱安定性 – 7/95 |
TM 2.3.41 | 基材の総ハロゲン含有量向け検査法 – 4/06 |
TM 2.3.42 | ソルダマスク – 溶剤と洗浄剤に対する抵抗 – 3/07 |
セクション 2.4 – メカニカル試験法 | |
---|---|
TM 2.4.1E
![]() |
接着性(密着性)、テーププルテスト – 5/04 |
TM 2.4.1.2 | ハイブリッド基板における導体の接着 – 12/87 |
TM 2.4.1.3 | 接着 抵抗器 (ハイブリッド回路) – 12/87 |
TM 2.4.1.4 | 接着 重ね塗り (ハイブリッド回路) – 12/87 |
TM 2.4.1.5A | 跡写りの測定 – 5/95 |
TM 2.4.1.6 | 接着 ポリマー塗膜 – 7/95 |
TM 2.4.2A | 銅はくの延性 – 3/76 |
TM 2.4.2.1D | 曲げ疲労と延性 フォイル – 3/91 |
TM 2.4.3E | 曲げ疲労 フレキシブルプリント配線材料 – 6/11 |
TM 2.4.3.1C | 曲げ疲労と延性 フレキシブルプリント配線 – 3/91 |
TM 2.4.3.2C | 曲げ疲労と延性 フレキシブルメタルクラッド誘導体 – 3/91 |
TM 2.4.4B | ラミネートの曲げ強度 (周囲温度) – 12/94 |
TM 2.4.4.1A | ラミネートの曲げ強度 (高温) – 12/94 |
TM 2.4.5 | 耐折強度 フレキシブルプリント配線材料 – 4/73 |
TM 2.4.5.1
![]() |
柔軟性 – コンフォーマルコーティング- 7/00 |
TM 2.4.6 | 熱油 – 4/73 |
TM 2.4.7A | 機械加工性 プリント配線材料 – 7/75 |
TM 2.4.7.1 | ソルダマスク – 機械加工性の測定 – 3/07 |
TM 2.4.8C | メタルクラッドラミネートの引きはがし強さ – 12/94 |
TM 2.4.8.1 | 引きはがし強さ 金属はく (薄積層向けキーホール法) – 1/86 |
TM 2.4.8.2A | 高温時のメタルクラッドラミネートの引きはがし強さ (熱流体法) – 12/94 |
TM 2.4.8.3A | 高温時のメタルクラッドラミネートの引きはがし強さ (熱空気法) – 12/94 |
TM 2.4.8.4 | キャリア開放 薄銅 – 1/90 |
TM 2.4.9E | 引きはがし強さ フレキシブル誘導体材料 – 6/14 |
TM 2.4.9.1 | フレキシブル回路の引きはがし強さ – 11/98 |
TM 2.4.9.2 | ボンディング行程 – 11/98 |
TM 2.4.11 | フレキシブル誘導体材料のせん断強さ – 4/73 |
TM 2.4.12A | はんだ付け性 エッジディップ法 – 6/91 |
TM 2.4.13F | はんだフロート抵抗 フレキシブルプリント配線材料 – 5/98 |
TM 2.4.13.1 | ラミネートの熱応力 – 12/94 |
TM 2.4.14 | 金属表面のはんだ性 – 4/73 |
TM 2.4.14.1 | はんだ性 ウェーブソルダーリング法 – 3/79 |
TM 2.4.14.2A
![]() |
液体フラックス活性 はんだぬれ性試験 – 6/04 |
TM 2.4.15A | 表面仕上げ 金属はく – 3/76 |
TM 2.4.16B | 起爆引き裂き強さ フレキシブル絶縁材料 – 3/14 |
TM 2.4.17 | 引き裂き強さ (伝搬) – 4/73 |
TM 2.4.17.1B | 伝搬引き裂き強さ フレキシブル絶縁材料 – 2/13 |
TM 2.4.18B | 引っぱり強度と伸び 銅はく – 8/80 |
TM 2.4.18.1A | 引っぱり強度と伸び インハウスメッキ処理 – 5/04 |
TM 2.4.18.2 | 熱破裂強度 はく – 7/89 |
TM 2.4.18.3 | 引っぱり強度、伸び、引っぱり応力 – 7/95 |
TM 2.4.19C | 引っぱり強度と伸び フレキシブルプリント配線材料 – 5/98 |
TM 2.4.20 | 端子ボンディング強度 フレキシブルプリント配線 – 4/73 |
TM 2.4.21E | ランドボンディング強度 無補強部品孔 – 5/04 |
TM 2.4.22C
![]() |
反りとねじれ (パーセンテージ) – 6/99 |
TM 2.4.22.1C | 胴曲がりとねじり – ラミネート – 5/93 |
TM 2.4.22.2 | 基板曲率: 溶着誘導体を伴うシリコンウエハース – 7/95 |
TM 2.4.23 | ラミネート材のソルダレジスト – 3/79 |
TM 2.4.24C | ガラス遷移温度と熱機械分析装置(TMA)によるZ軸の熱膨張 – 12/94 |
TM 2.4.24.1 | 熱剥離試験 (TMA 法) – 12/94 |
TM 2.4.24.2 | 有機膜のガラス遷移温度 – 動的機械分析(DMA)法 – 7/95 |
TM 2.4.24.3 | 有機膜のガラス遷移温度 – TMA 法 – 7/95 |
TM 2.4.24.4 | 高密度相互接続 (HDI) とマイクロビアに使用される材料のガラス遷移と引っぱり応力 - DMA 法 – 11/98 |
TM 2.4.24.5 | 高密度相互接続 (HDI) とマイクロビアに使用される材料のガラス遷移温度と熱膨張 -TMA 法 – 11/98 |
TM 2.4.24.6 | 熱分量分析(TGA)を利用したラミネート材の熱分解温度(Td) – 4/06 |
TM 2.4.25C | 示差走査熱量測定(DSC)による、ガラス遷移温度と加硫要素 – 12/94 |
TM 2.4.26 | アディティブプリント基板向けテープ試験 – 3/79 |
TM 2.4.27.1B | 摩耗 (テーバ式) ソルダマスクとコンフォーマルコーティング – 1/95 |
TM 2.4.27.2A | ソルダマスク摩耗 (鉛筆法) – 2/88 (確認済) |
TM 2.4.28B | 接着 ソルダマスク (非溶融金属) – 8/97 |
TM 2.4.28.1F
![]() |
ソルダマスクの密着性 – テーププルテスト方法 – 3/07 |
TM 2.4.29C | 接着 ソルダマスク フレキシブル回路 – 3/07 |
TM 2.4.30 | 耐衝撃性 ポリマーフィルム – 10/86 |
TM 2.4.31A | 折り フレキシブルフラットケーブル – 4/86 |
TM 2.4.32A | 折り曲げ型温度試験 フレキシブルフラットケーブル – 4/86 |
TM 2.4.33C | 曲げ疲労と延性 フラットケーブル – 3/91 |
TM 2.4.34 | はんだペースト粘性 – Tバースピン スピンドル法(300,000?1,600,000 センチポアズに適用) – 1/95 |
TM 2.4.34.1 | はんだペースト粘性 – Tバースピンドル法 (300,000 センチポアズ未満に適用) – 1/95 |
TM 2.4.34.2 | はんだペースト粘性 – スパイラルポンプ法 (300,000?1,600,000 センチポアズに適用) – 1/95 |
TM 2.4.34.3 | はんだペースト粘性 – スパイラルポンプ法 (300,000 センチポアズ未満に適用) – 1/95 |
TM 2.4.34.4 | ペーストフラックス粘性 – Tバースピンドル法 – 1/95 |
TM 2.4.35 | はんだペースト – スランプ試験 – 1/95 |
TM 2.4.36C | リワークシミュレーション 有鉛部品向けスルーホール – 5/04 |
TM 2.4.37A | 端子接続向け手付けはんだ工具の評価 – 7/91 |
TM 2.4.37.1A | プリント配線基板印加向け手付けはんだ工具の評価 – 7/91 |
TM 2.4.37.2 | 重度の熱負荷に対する手付けはんだ工具の評価 – 7/93 |
TM 2.4.38A | プリプレグスケールフロー試験 – 6/91 |
TM 2.4.39A | 寸法安定性 ガラス強化薄積層 – 2/86 |
TM 2.4.40 | 多層プリント基板の内層ボンディング強度 – 10/87 |
TM 2.4.41 | 電気的絶縁回路の線形熱膨張係数 – 3/86 |
TM 2.4.41.1A | 石英ガラス(クオーツ)による熱膨張係数 膨張計法 – 8/97 |
TM 2.4.41.2A | 熱膨張係数 – ストレインゲージ法 – 5/04 |
TM 2.4.41.3 | 面内熱膨張係数 有機膜 – 7/95 |
TM 2.4.41.4 | 体積熱膨張 無機基板のポリマー塗膜 – 7/95 |
TM 2.4.42 | チップ接着剤のねじれ強さ – 2/88 |
TM 2.4.42.1 | 接着剤の高温機械強度保持 – 3/88 |
TM 2.4.42.2 | ダイのせん断強度 – 2/98 |
TM 2.4.42.3 | ワイヤボンディング引っぱり強度 – 2/98 |
TM 2.4.43 | はんだペースト – はんだボール試験 – 1/95 |
TM 2.4.45 | はんだペースト – はんだぬれ性試験 – 1/95 |
TM 2.4.46A | 広がり試験 液体または抽出はんだ付け用フラックス はんだペーストと抽出心線または中間加工 – 6/04 |
TM 2.4.47 | フラックス残渣乾燥度 – 1/95 |
TM 2.4.48 | フラックス入りワイヤはんだのすり割り – 1/95 |
TM 2.4.49 | はんだプール試験 – 1/95 |
TM 2.4.50 | 熱伝導度 ポリマーフィルム – 7/95 |
TM 2.4.51 | 自己シミング熱伝導接着剤 – 1/95 |
TM 2.4.52 | 基材向け樹脂系の破壊靭性 – 10/13 |
セクション 2.5 – 電気的試験法 | |
---|---|
TM 2.5.1B | プリント配線板材料のアーク抵抗 – 5/86 |
TM 2.5.2A | 絶縁材料のキャパシタンス – 7/75 |
TM 2.5.3B | ブレークダウン電流 めっきスルーホール – 8/97 |
TM 2.5.4 | 電流容量 多層プリント配線 – 4/73 |
TM 2.5.4.1A | 導体の電流変化による導体温度上昇 – 8/97 |
TM 2.5.5A | プリント配線材料の誘電率 – 7/75 |
TM 2.5.5.1B | 電極系に1MHz に接触する絶縁材料の誘電率と損失正接(損失係数) – 5/86 |
TM 2.5.5.2A | プリント配線基板材料の誘電率と損失係数–クリップ式 – 12/87 |
TM 2.5.5.3C | 材料の誘電率と損失正接(損失係数) (二液電池式) – 12/87 |
TM 2.5.5.4 | プリント配線基板材料の誘電率と損失係数–マイクロメータ法 – 10/85 |
TM 2.5.5.5C | Xバンドにおける誘電率と損失正接(損失係数)のストリップライン試験 – 3/98 |
TM 2.5.5.5.1 | 14GHZに対する回路基板材料の複素比誘電率向けストリップライン試験 – 3/98 |
TM 2.5.5.6 | クラッドラミネートの誘電率向け非破壊全薄板共振試験 – 5/89 |
TM 2.5.5.7A | 時間領域反射測定(TDR)によるプリント基板上の特性インピーダンス – 3/04 |
TM 2.5.5.8 | 低周波誘電率と損失正接 ポリマーフィルム – 7/95 |
TM 2.5.5.9 | 誘電率と損失正接 平行板 1MHz?1.5 GHz – 11/98 |
TM 2.5.5.10 | 埋込型不動態材料の誘電率と損失正接を測定する高周波試験 – 7/05 |
TM 2.5.5.11 | 時間領域反射測定(TDR)によるプリント基板上の伝搬遅延線 – 4/09 |
TM 2.5.5.12A | プリント基板の信号損失量を測定する試験法 – 7/12 |
TM 2.5.5.13 | スプリットシリンダ共振回路を利用した比誘電率と損失正接 – 1/07 |
TM 2.5.6B | 硬質プリント配線材料の誘電破壊 – 5/86 |
TM 2.5.6.1B | ソルダマスク – 絶縁耐力 – 3/07 |
TM 2.5.6.2A | プリント配線材料の電気強度 – 3/98 |
TM 2.5.6.3 | 誘電破壊電圧と絶縁耐力 – 10/86 |
TM 2.5.7D | 誘電体耐圧 プリント基板 – 5/04 |
TM 2.5.7.1
![]() |
耐電圧 – 高分子(ポリマー)コンフォーマルコーティング – 7/00 |
TM 2.5.7.2A | 誘電体耐圧 (高電位法) – プリント基板向け薄誘電層 – 11/09 |
TM 2.5.8A | フレキシブルプリント配線材料の損失係数 – 7/75 |
TM 2.5.10.1 | 接着剤相互接続ボンドの絶縁抵抗 – 11/98 |
TM 2.5.12 | 相互接続抵抗 多層プリント配線 – 4/73 |
TM 2.5.13A | 銅はくの抵抗 – 3/76 |
TM 2.5.14A | 銅はくの固有抵抗 – 8/76 |
TM 2.5.15A | フラットケーブルのRFI/EMIシールディング用試験方法ガイドライン – 10/86 |
TM 2.5.16A | ショート 多層プリント配線の内部 – 11/88 |
TM 2.5.17E | プリント配線材料の体積抵抗率と表面抵抗率 – 5/98 |
TM 2.5.17.1A | 誘電体材料の体積・表面抵抗率 – 12/94 |
TM 2.5.17.2 | 高密度相互接続 (HDI) とマイクロビアに使用される導体材料の体積抵抗率 2線式 – 11/98 |
TM 2.5.18B | 特性インピーダンス フラットケーブル (不平衡) – 7/84 |
TM 2.5.19A | 時間領域反射率計(TDR)を使用したフラットケーブルの伝搬遅延 – 7/84 |
TM 2.5.19.1A | 2重掃引オシロスコープを使用したフラットケーブルの伝搬遅延 – 7/84 |
TM 2.5.21A | デジタル不平衡クロストーク フラットケーブル – 3/84 |
TM 2.5.24 | 導体抵抗 フレキシブルフラットケーブル – 6/79 |
TM 2.5.25A | 誘電体耐圧 フレキシブルフラットケーブル – 11/85 |
TM 2.5.26A | 絶縁抵抗 フレキシブルフラットケーブル – 11/85 |
TM 2.5.27 | プリント配線基板材料素板の表面絶縁抵抗 – 3/79 |
TM 2.5.28A | Q共振 フレキシブルプリント配線材料 – 4/88 |
TM 2.5.30 | 平衡および不平衡ケーブルの減衰測定 – 12/87 |
TM 2.5.31 | 電流漏れ (重ね塗りフィルムを介して) – 12/87 |
TM 2.5.32 | 抵抗試験 スルーホールめっき – 12/87 |
TM 2.5.33 | 手はんだ付ツールによる電気的オーバーストレスの測定 – 11/98 |
TM 2.5.33.1 | 手はんだ付ツールによる電気的オーバーストレスの測定 – 接地測定 – 11/98 |
TM 2.5.33.2 | 手はんだ付ツールによる電気的オーバーストレスの測定 – 過度測定 – 11/98 |
TM 2.5.33.3 | 手はんだ付ツールによる電気的オーバーストレスの測定 – 電流漏れ測定 – 11/98 |
TM 2.5.33.4 | 手はんだ付ツールによる電気的オーバーストレスの測定 – 遮蔽エンクロージャ – 11/98 |
TM 2.5.34 | 内蔵型抵抗器向け負荷抵抗定格 – 7/12 |
セクション 2.6 – 環境試験法 | |
---|---|
TM 2.6.1G | 耐菌性 プリント配線材料 – 3/07 |
TM 2.6.1.1
![]() |
カビ抵抗性– コンフォーマルコーティング – 7/00 |
TM 2.6.2D | 吸湿 フレキシブルプリント配線 – 2/12 |
TM 2.6.2.1A | 吸湿 メタルクラッド プラスチックラミネート – 5/86 |
TM 2.6.3F | 耐湿性・絶縁抵抗 プリント基板 – 5/04 |
TM 2.6.3.1E | ソルダマスク – 耐湿性・絶縁抵抗 – 3/07 |
TM 2.6.3.2B | 耐湿性・絶縁抵抗 フレキシブルベース層誘導体 – 5/88 |
TM 2.6.3.3B
![]() |
表面絶縁抵抗、フラックス – 6/04 |
TM 2.6.3.4A
![]() |
耐湿性および絶縁抵抗– コンフォーマルコーティング – 7/03 |
TM 2.6.3.5 | 表面絶縁抵抗別ベア基板洗浄度 – 1/04 |
TM 2.6.3.6 | 表面絶縁抵抗 – フラックス – 遠隔通信 – 1/04 |
TM 2.6.3.7 | 表面絶縁抵抗 – 3/07 |
TM 2.6.4B | ガス放出 プリント基板 – 5/04 |
TM 2.6.5D | 物理的衝撃 多層プリント配線 – 5/04 |
TM 2.6.6B | 温度サイクル試験 プリント配線基板 – 12/87 |
TM 2.6.7A | 熱衝撃と導通 プリント基板 – 8/97 |
TM 2.6.7.1A
![]() |
熱衝撃 – コンフォーマルコーティング – 7/00 |
TM 2.6.7.2C
![]() |
熱衝撃、熱サイクルおよび導通 – 3/20 |
TM 2.6.7.3 | 熱衝撃 – ソルダマスク – 7/00 |
TM 2.6.8E | 熱応力 メッキスルーホール – 5/04 |
TM 2.6.8.1 | 熱応力 ラミネート – 9/91 |
TM 2.6.9B | 振動 硬化プリント配線 – 5/04 |
TM 2.6.9.1
![]() |
超音波エネルギーに対する電子組立品の感度判定試験 – 1/95 |
TM 2.6.9.2
![]() |
超音波エネルギーに対する電子部品の感度判定試験 – 1/95 |
TM 2.6.10A | X線(放射線写真) 多層プリント配線基板試験法 – 8/97 |
TM 2.6.11B | 加水分解安定性 ソルダマスクあるいはコンフォーマルコーティング – 8/98 |
TM 2.6.11D | ソルダマスク – 加水分解安定性 – 3/07 |
TM 2.6.11.1
![]() |
加水分解安定性 – コンフォーマルコーティング – 7/00 |
TM 2.6.12 | 温度試験 フレキシブルフラットケーブル – 6/79 |
TM 2.6.13 | 金属デンドライト成長に対する感受性評価: コーティングを施さないプリント配線 – 10/85 |
TM 2.6.14D | ソルダマスク – 電気化学的移動に対する抵抗 – 3/07 |
TM 2.6.14.1
![]() |
電気化学的マイグレーション耐性検査 – 9/00 |
TM 2.6.15C
![]() |
腐食 フラックス – 6/04 |
TM 2.6.16 | ガラスエポキシ ラミネート整合性向け圧力容器法 – 7/85 |
TM 2.6.16.1 | 高温および圧力下(圧力容器)における高密度相互接続 (HDI) 材料の耐湿性 – 8/98 |
TM 2.6.17 | 加水分解安定性 フレキシブルプリント配線材料 – 12/82 |
TM 2.6.18A | 低温フレキシブル フレキシブルプリント配線材料 – 7/85 |
TM 2.6.19 | ハイブリッドセラミック 多層基板ボードの環境試験および絶縁抵抗試験 – 12/87 |
TM 2.6.21B | メタルクラッド フレキシブルラミネート、カバー材料、接着剤ボンディングフィルムの使用温度 – 6/11 |
TM 2.6.23 | 蒸気エージャー温度再現性向け試験手順 – 7/93 |
TM 2.6.24 | 環境条件下における接合部安定性 – 11/98 |
TM 2.6.25C
![]() |
耐CAF(Conductive Anodic Filament)性評価試験:X-Y 軸 – 2/21 |
TM 2.6.26A | 直流電流誘導 温度サイクリング試験 – 6/14 |
TM 2.6.27b
![]() |
熱応力、対流リフロー組立によるシミュレーション – 2/20 |
TM 2.6.28 | 水分および吸湿度 (バルク) プリント基板 – 8/10 |