こて先の選定基準と基礎知識

こて先の選定基準と基礎知識
1) 基本形状
はんだ付箇所、基板のランドと部品の電極の形状、その接点に最大接触するこて先の形状を選定する。IC用の特殊形状もある。
2) 侵入角
部品形状、電子組立品の状態、基板の部品配置や設計状況によって、正面から最適な接触が得られない場合は、こて先の角度を調整した形状が必要。
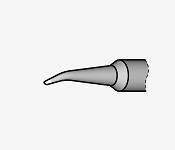
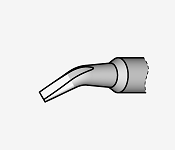
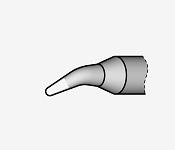
先端が曲がったこて先例
ベントタイプ使用例
通常のストレートタイプで可能なはんだ付箇所であっても、手首の感覚や安定姿勢が難しい箇所などでベントタイプのこて先を使用するとより、はんだ付け作業が楽に正確に行える。特にIリード、Jリード部品に有利。
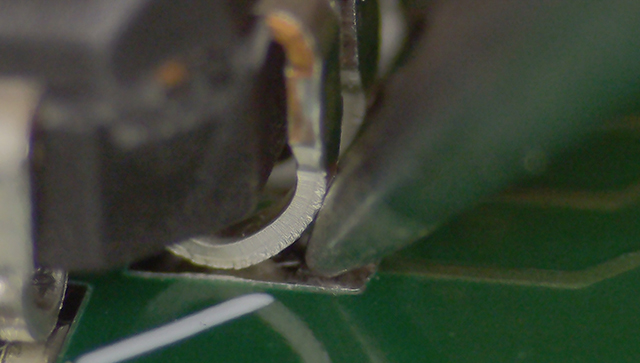
本来は、もっとこて先を寝かせると、より接触面が広がる
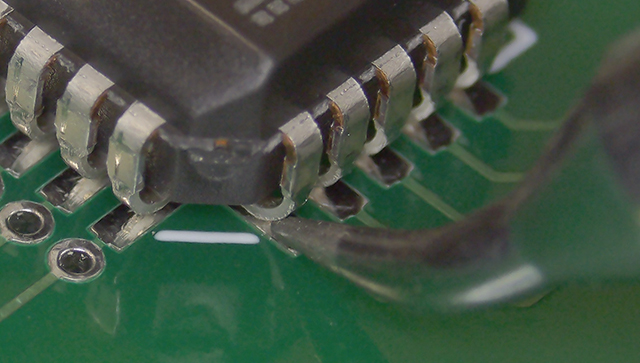
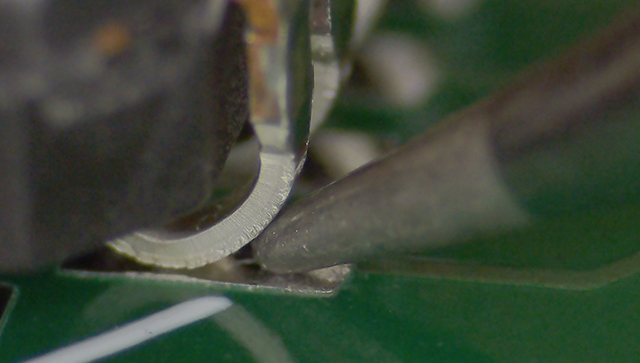
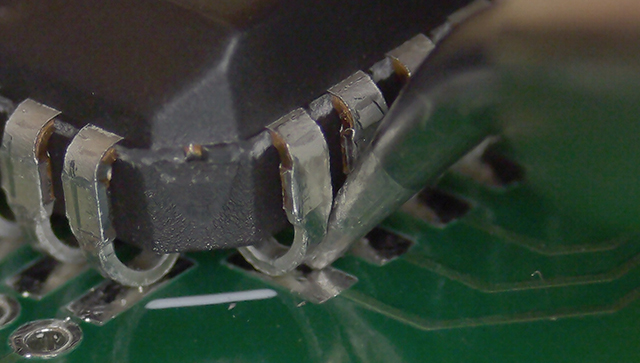
ベントタイプを使用することで、同じ姿勢であってもより深くこて先が入り接触面が広くなっていることが分かる。最右図は、ピンのサイド面や裏面へぬれが必要な場合、ベントタイプを立てて使用することで応用できる。
3) 熱容量
形状、こて先が侵入出来ても、部品や基板パターン、サーマルプレーンなど、必要な熱容量により適した温度を維持できない場合があります。この場合、より蓄熱の大きい形状のこて先を選びます。
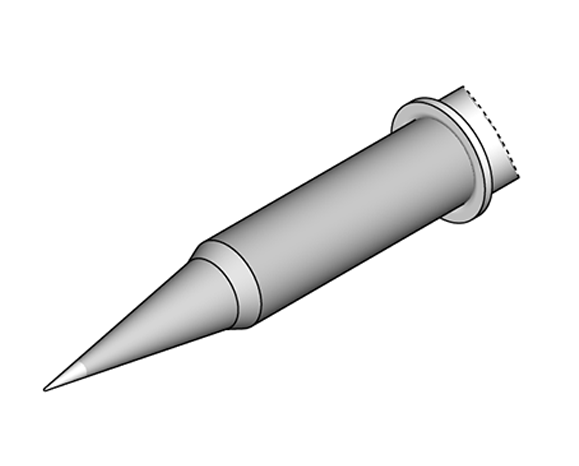
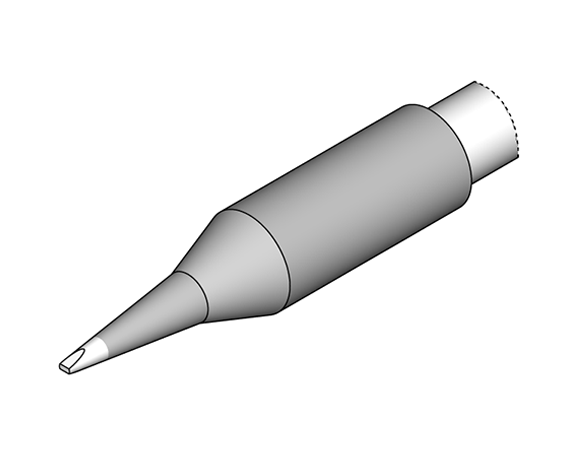
通常熱容量
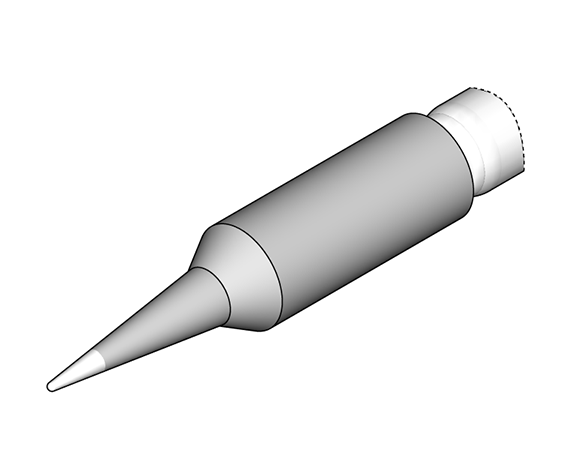
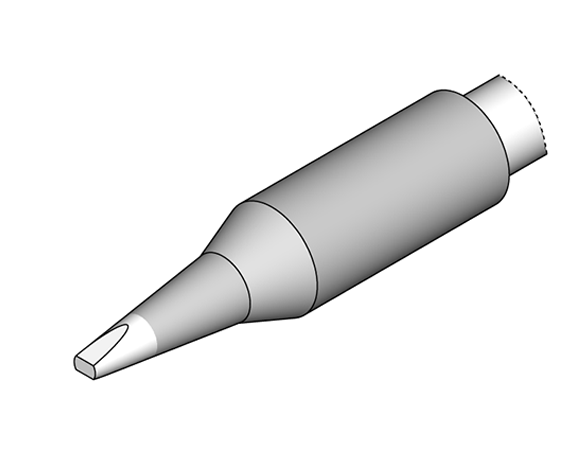
高熱容量タイプ
そもそも何故、はんだが付くのか?
表面が清浄な金属と金属(一般的には銅)の隙間に熔融したはんだ合金を流しこみ、はんだのぬれ、銅と錫の原子が拡散して金属間化合物が生成されます。これが電子機器に対するはんだ付です。
” はんだ付部位へ適切に熱を伝達する” が、こて先に与えられた最も重要な役割となります。そのため、適切に熱を伝達する正しい”こて先”が必要です。
はんだ付に必要な条件は、温度とこて先以外にもはんだの金属組成、フラックスの性能も必要です、しかしここでは、熱を伝えるこて先の選定法を重点に解説します。
熱伝達に重要な要件とは?
図3) こて先の温度差
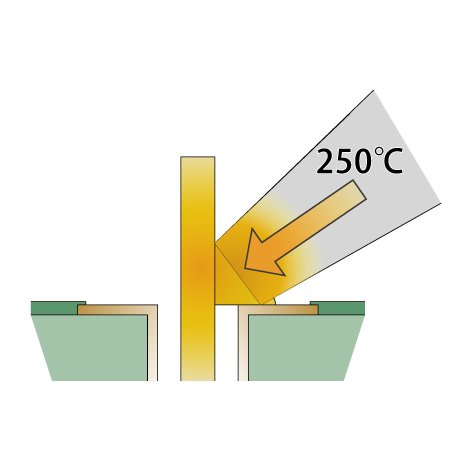
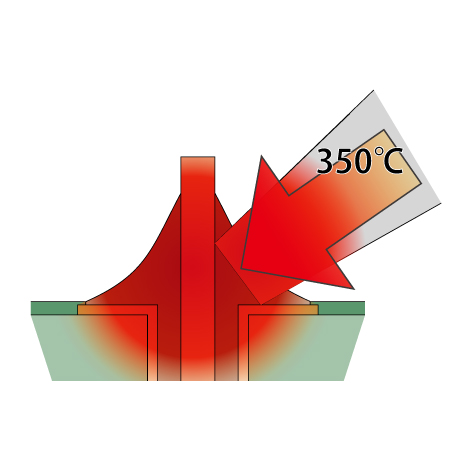
図4) 接触面積:こて先幅とランド幅
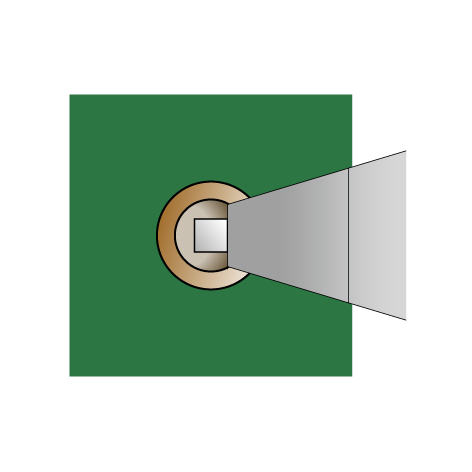
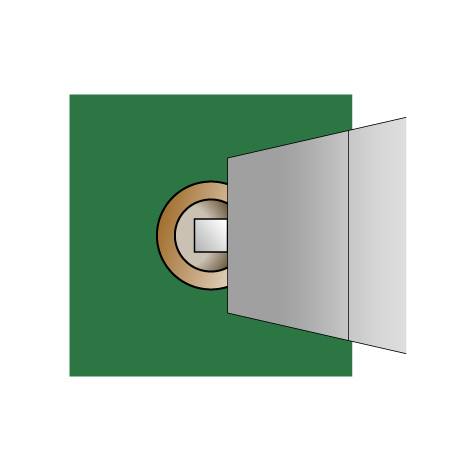
図5) 接触面積:ヒートブリッジ
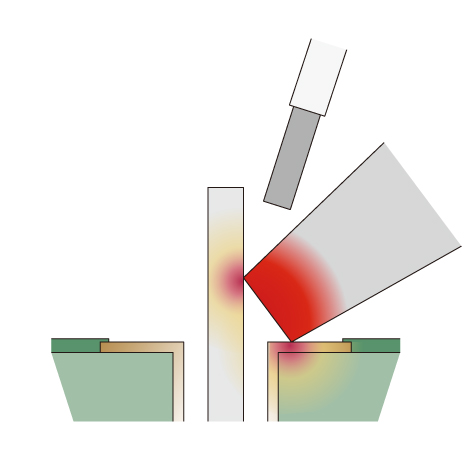
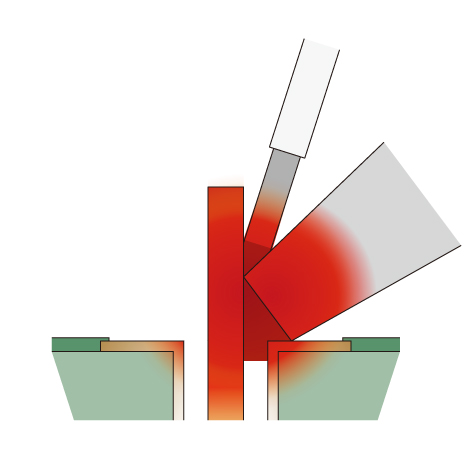
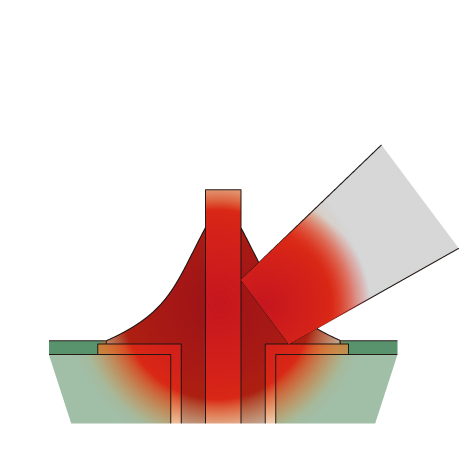
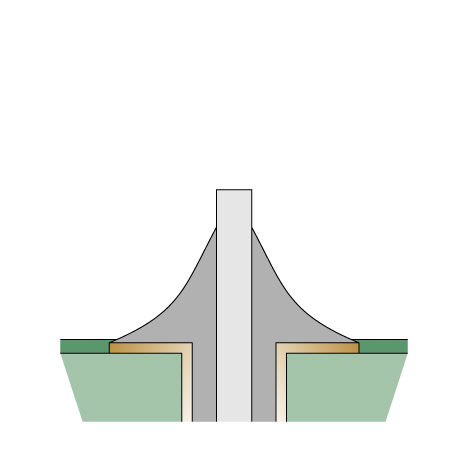
1) 温度差
こて先の温度差に注意!こて先の温度が高いほど、熱は多く・素早く対象部位へ伝達します。しかし各デバイスには耐熱特性があり、限界がある上に、高温のはんだごてでは、作業性にも様々な問題を引き起こします。そのため、鉛フリーはんだでは350℃、鉛入り(共晶はんだ)では330℃が適正温度とされています。
はんだ付けを無理なく行うには、はんだ材の融点+100~150℃にこて先温度を設定するのが良い。こて先をあて、予備はんだを加え(ヒートブリッジ、図3-2)本はんだ付けを行う。こて先温度を高くしすぎると、パターンを損傷したり、フラックス活性度が悪くなり、はんだ付けには適さない。適温にてはんだが出来ない場合は、こて先の熱容量不足、熱回復力、ヒーターの能力不足のいずれかに該当します。
温度差:こて先温度 (図3)(図3-1) こて先温度が低くてもはんだ付けは出来ない。温度差が小さいと熱量の伝わりが遅く、時間をかけても必要な温度まで達しない。 (図3-2) こて先温度は一般的に約350℃がもっとも熱が勢いよく伝わり、最適な温度です。
2) 接触面積
こて先と部品との接触面積が重要!熱伝達元であるこて先と部品電極面の接触面積で、伝わる熱量が変わってきます。そのため、各部品形状やタイプごとに最適な接触面積があります。
接触面積:こて先の幅 (図4)(図4-1)ランド幅に対して、適したこて先幅で、熱伝達が効率的で十分な接触面積を確保できる。
- IPC J-STD-001によるとこて先幅とランド幅が同等程度が推奨とされている。
(図4-2)こて先の幅が大きすぎて、熱伝達が効率的でなく、ランド周辺を損傷させる、余分なはんだ屑(FOD)を残留させる可能性大
接触面積:ヒートブリッジ (図5)(図5-1)こて先をあてた瞬間は、点接触で充分に熱は伝わらない (図5-2)少しはんだを加える(予備はんだ)と、流体化したはんだにより接触面積が大きくなり、ヒートブリッジによって急速にはんだの接触箇所に熱が伝わる (図5-3)十分に熱が伝わったところで、本はんだを追加する (図5-4)こて先を外し、冷却する