Iron tip method
“Iron tip / Contact soldering method”
Know & understand the basic of basics
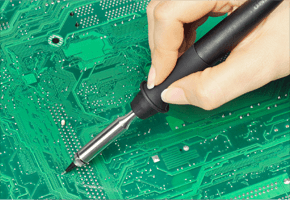
– The most mature soldering method, with hundreds years history –
Among all kinds of soldering methods, iron tip/contact soldering is the method with the longest history, and is also technically the most established. It was mainly done by hands, but soldering robots have rapidly advanced its automation and rationalization in recent years. Understanding the basics of iron tip, contact soldering is the key to improve any types of soldering automation and technology. Here is the basic of iron tip, contact soldering method to start your soldering improvement journey.
– The history of iron tip soldering since 19th century –
Soldering itself has a history of 6000 years, and iron tip soldering was already in 1860’s. Burning iron tip soldering was the main method at that time. It was replaced by electric tip during the 1920s, around the time radio broadcasting began. The currently used ordinary soldering tips with temperature control functions began to be used in the 1960s, in conjunction with the invention of printed PCBs and transistors. That was around the time when people became aware of the vulnerability of transistors to heat and the importance of soldering tip temperature control.
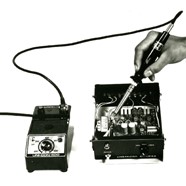
UNIX The first temperature controlled soldering station
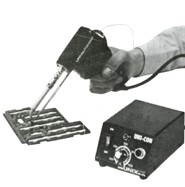
With manually solder feeding mechanism
– Basic principles of soldering –
The soldering bonding process begins when flux is used to remove the oxide skin from the substrate. The bond is then formed by “wetting”, “melting”, and “spreading” on the interface between the substrate and the solder. The molten solder expands onto the metallic surface from which the oxide skin was removed, and the substrate metal melts into the solder material.
[Melting]: In the metallic material melting process, a metallic alloy is formed from the reciprocal migration of atoms from both the solder material and the substrate.
[Spreading]: A solder metallic bond is achieved by melting and spreading, but at the same time, care must be taken to address metallic reaction phenomena so they do not reduce the solder quality.
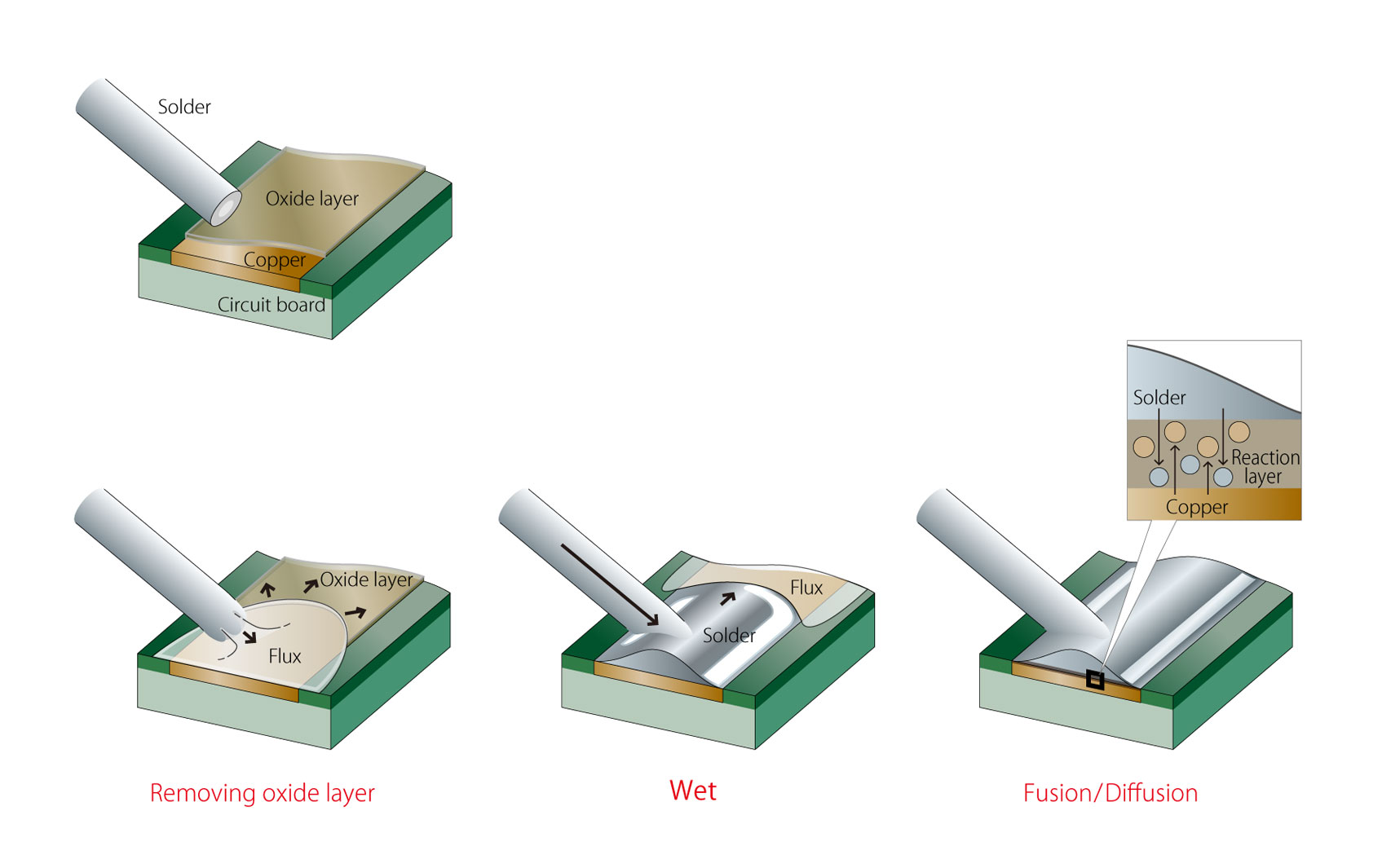
The melting and spreading processes result in the formation of an intermetallic bond in the solder. However, the operator must carefully address and prevent metallic reaction phenomena that can decrease solder quality. An incorrect temperature during the process of attaching a component to a PCB can lead to a thickening of the intermetallic alloy that can weaken the bond.
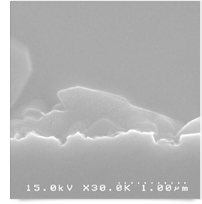
Condition of the compound 30,000 X
(appropriate temp.)
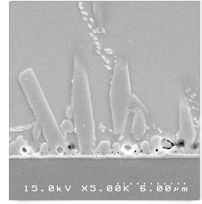
Condition of IMC with hypertrophic needles 5,000 X
(excessive heat)
- Tin, solder’s main ingredient, demonstrates its strong tendency to dissolve other metals with which it comes into contact. Lead-free solder with a high proportion of tin tends to dissolve, or when a PCB is soaked during flow soldering, the substrate metal and copper corrode and flow into the solder. In either case the impurity level may easily rise.
- Enables the best quality soldering in term of strength and reliability
- The solder for operation is a 100% completely new
- There is little heat damage. It can be used to solder electronic components that are vulnerable to heat
- The equipment is compact and inexpensive, it is easy to adopt.
– Bond strength and reliability. Tip soldering for best quality –
The biggest advantage of iron tip/contact soldering is that it can provide the highest quality. The quality of soldering is determined by two factors: bond strength and reliability. New and genuine solder is continuously supplied for tip soldering. With flow soldering processing, the substrate metal melts into the molten solder and its properties then change. The inflow of impurities is recognized as a major cause of reduced bond strength.
– Heat damage to the component is kept to the absolute minimum by instant heat transfer –
With iron tip soldering, the component is subject to heating for a short time, generally within 2 seconds. Electronic components can be attached without reducing their performance because of little heat transfer. The contact point is 1mm-5mm when compared with reflow soldering that adds heat to the whole assembly. The amount of transferred heat is very small, and there is no heat impact.
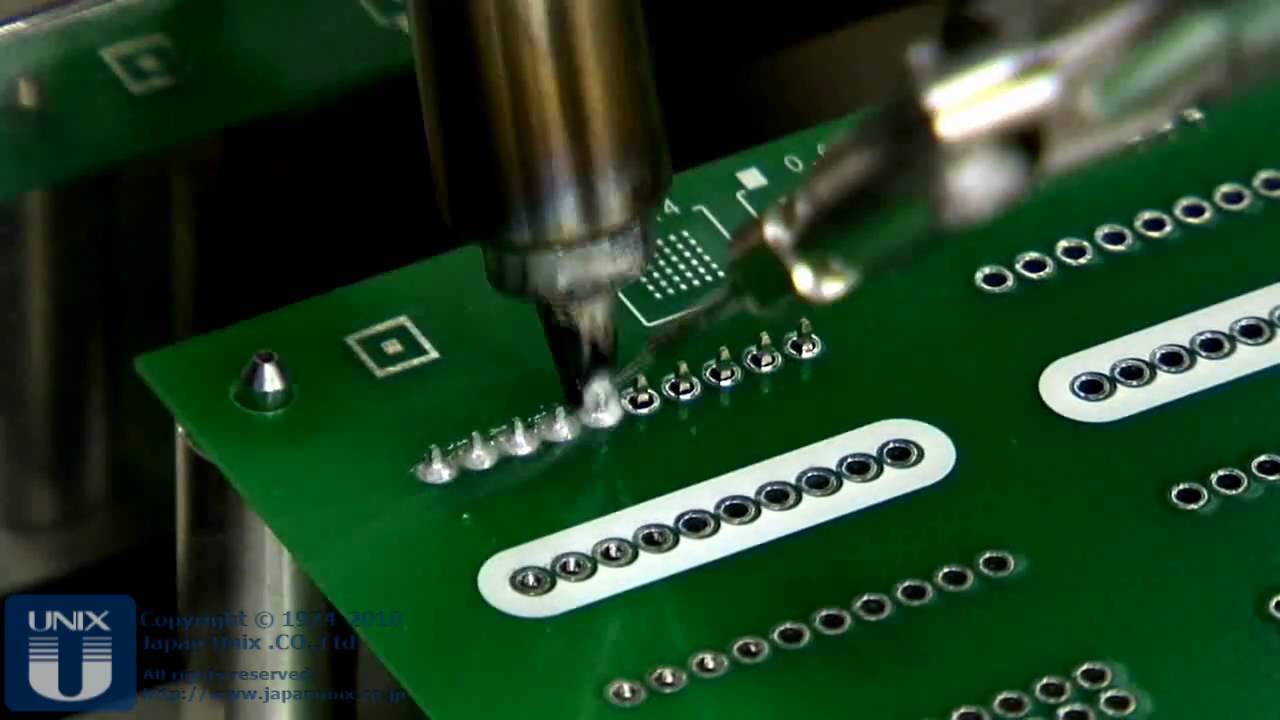
Robotic soldering
Automatic soldering robot High speed point solder
Point soldering that is also a basic. High-speed and reliable soldering attachment by a specialized robot
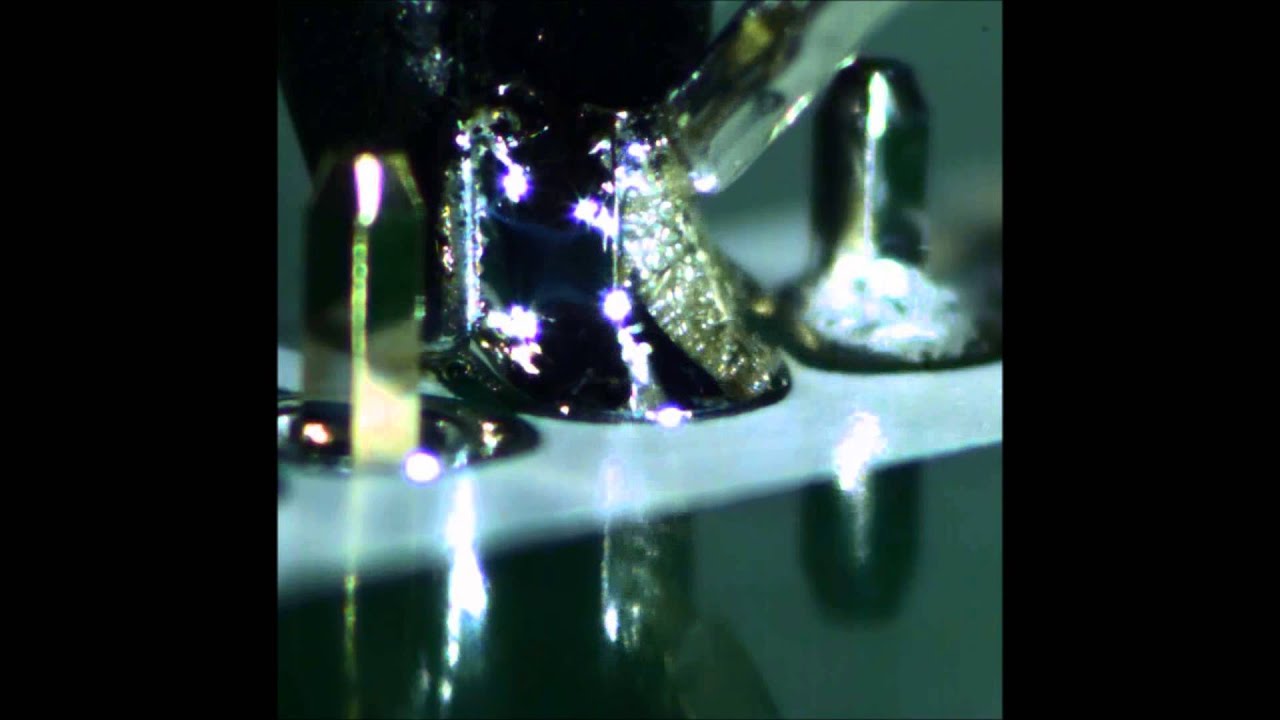
Robotic soldering
Automatic soldering robot High speed camera
View of tip soldering using a high speed camera Fundamental principle of soldering can be understood.
– Traditional work method with reliability and stability –
Iron tip soldering / contact soldering has the longest history of any other soldering methods, and it is the one with the most well-established strength and reliability. Iron tip soldering cannot easily handle some new kinds of work, resulted from recent technological advances. To handle the new requirements, new methods must be introduced, soldering theory must be fully understood, and the special characteristics of the new method must be exploited appropriately.