Basic Knowledge of Soldering Technology Vol.1 “Iron Tip Soldering”
Iron Tip soldering is the oldest, most technically mature, and most reliable of all soldering techniques. The three advantages of soldering with an iron tip and the criteria for selection from other soldering methods are explained.
Reliable traditional construction methods
Iron Tip soldering is a traditional technique with a history of several hundred years. It is the oldest of all soldering techniques utilized and is a technically established and mature basic method that boasts high joint strength and material reliability.
Soldering is achieved through a bonding process in which molten solder spreads (wetting) on a metal surface that has had its oxide film removed by a flux (soldering accelerator), the metal components of the base material dissolve into the solder components, and intermetallic compounds are formed by the mutual movement of solder material and base metal atoms (diffusion). This is achieved through a bonding process.
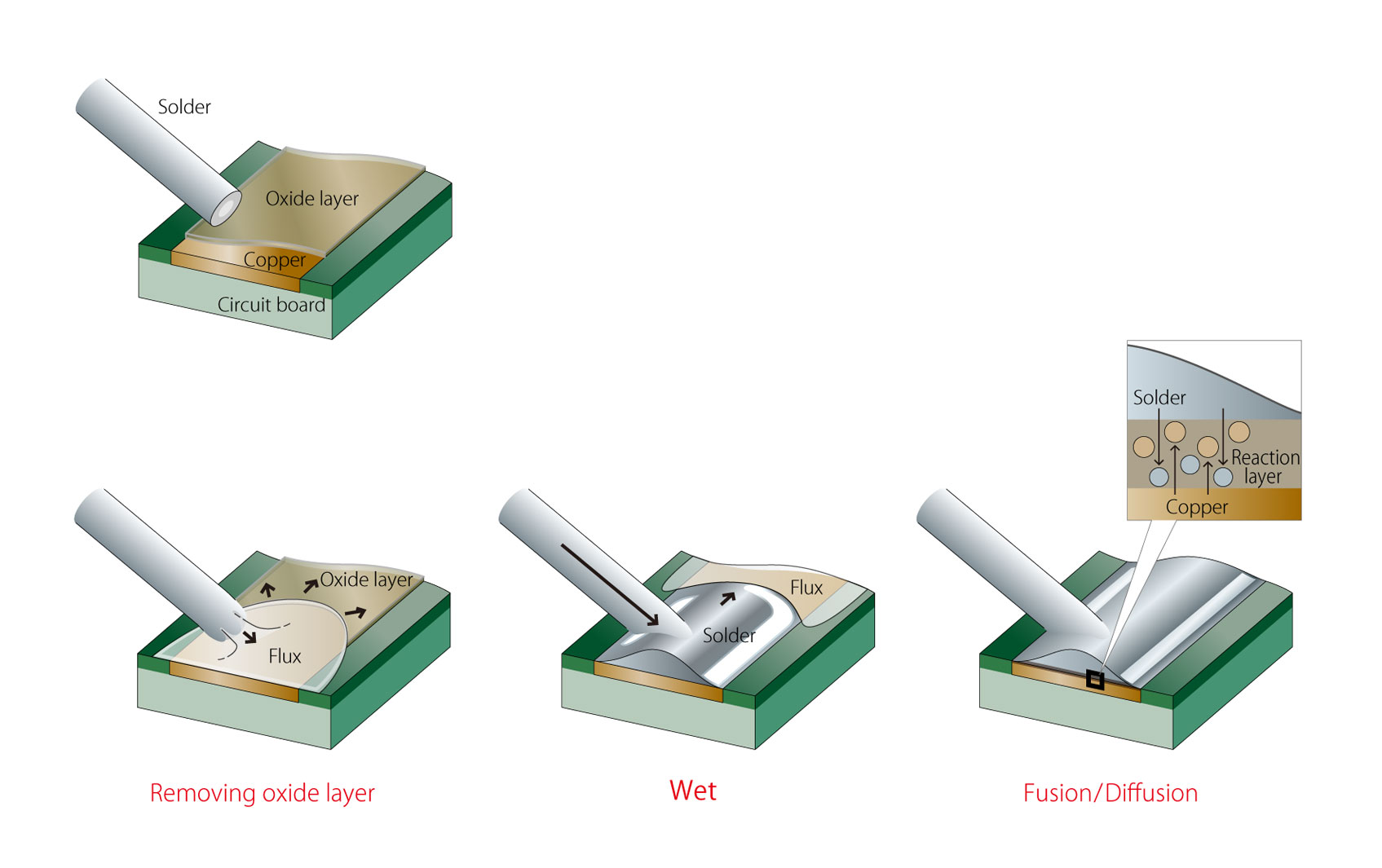
Features of Iron Tip soldering
(1) Highest quality soldering
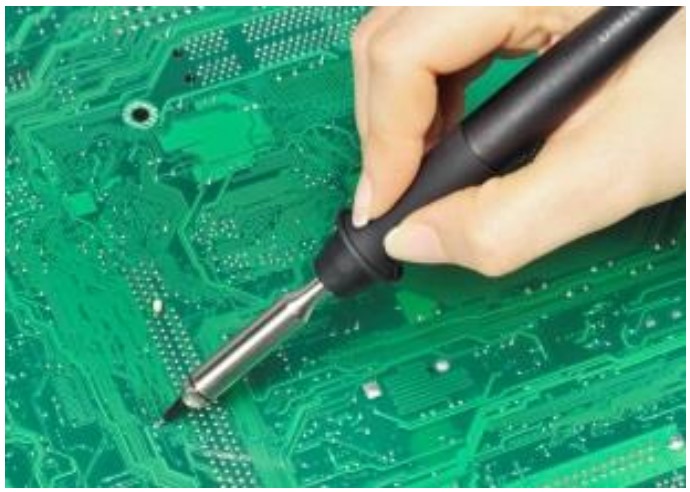
In iron tip soldering, a heated soldering iron with feeding wire solder to make a point-by-point joint, so new, pure solder is always used. Compared to any other soldering method, this method provides the “highest quality soldering” with the highest and most stable joint strength and reliability.
(2) No thermal damage to electronic components
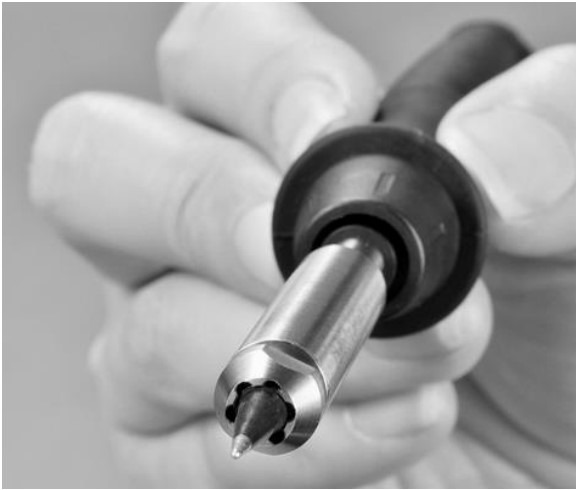
The advantage of iron tip soldering over reflow soldering is that it does not cause thermal damage to electronic components. In iron tip soldering, the time that the component is exposed to heat is generally less than 2 seconds, and since no thermal damage is caused to the electronic component, it can be mounted without degrading the performance of the electronic component. Reflow soldering uses a heating furnace to melt the solder, which causes a small amount of thermal damage to the electronic components.
(3) Impurities do not easily mix with solder
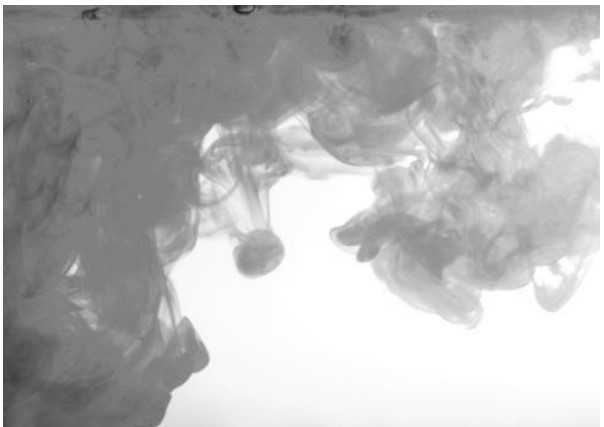
The advantage of iron tip soldering over flow soldering is that it is less affected by impurities. In soldering with an iron, a heated soldering iron with feeding wire solder to make a point-by-point joint, so new, pure solder material is always used. In flow soldering, the hot solder material is used continuously for days or weeks, causing impurities such as gold and copper from the board and components to dissolve into the solder and change its composition. The dissolution of these impurities leads to reduced solder strength and shortened durability life.
Select the construction method that best suits your purpose.
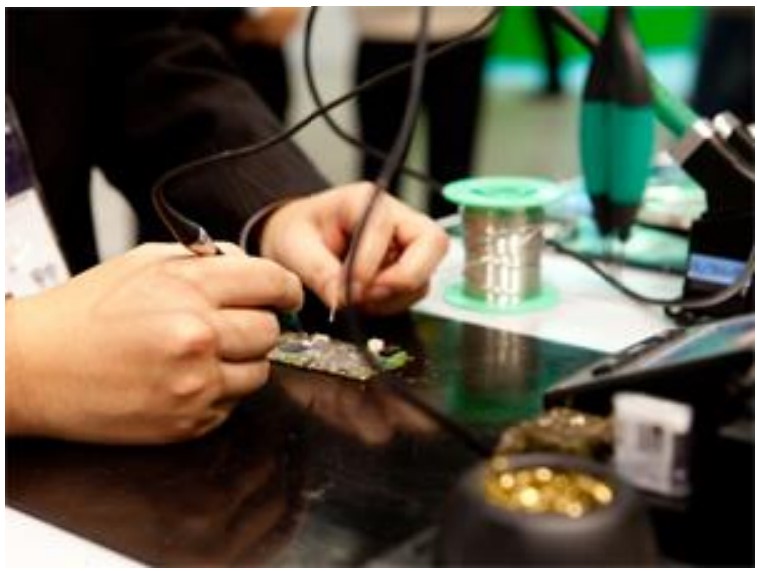
Another advantage of iron tip soldering is that there is a wide variety of tips and wire solder available, allowing for flexible selection according to the application. For example, for components with high heat capacity, using a tip with a high heat storage capacity enables soldering with high joint strength.
While iron soldering is an excellent method, other methods, such as flow/reflow soldering for mass production and laser soldering for non-contact joining of ultra-fine components, are also indispensable for modern production sites. It is important to understand the characteristics of each method before selecting the most suitable one.
To learn more about the history and strengths of soldering with an iron and how it differs from other soldering techniques, click here to download PDF files.