The Flow of Request
Processes from your inquiry to automation startup
After receiving a soldering inquiry from a customer, we formulate the necessary conditions, adjust and ship the product, and assist in the start-up of the production line to help maintain a stable production system. Throughout this entire process, it is the professionals in each field at Japan Unix who walk along side the customer. We are happy to answer any questions you may have about soldering. First of all, please feel free to contact us.
1. Inquiry

We are happy to answer any questions you may have about soldering, such as “Soldering is not going well,” or “Automation is working, but quality is not stable”. Japan Unix’s professional staff, who have a wealth of experience in soldering and automation, will be the first to respond to your inquiries. We will respond to even the most vague concerns and questions about soldering with a wealth of knowledge and sincerity. Please feel free to contact us. You can contact us by phone or by clicking the button below.
2. Initial Business Meeting

If, as a result of your inquiry, you request our assistance, we will set up an initial business meeting. At this time, the customer will be met by our sales staff, who have extensive knowledge in the manufacturing field. Based on our expertise in the customer’s industry and sector, we will make the most appropriate proposal in light of past cases, experience, and the latest technology and knowledge.
3. Testing and Demonstration
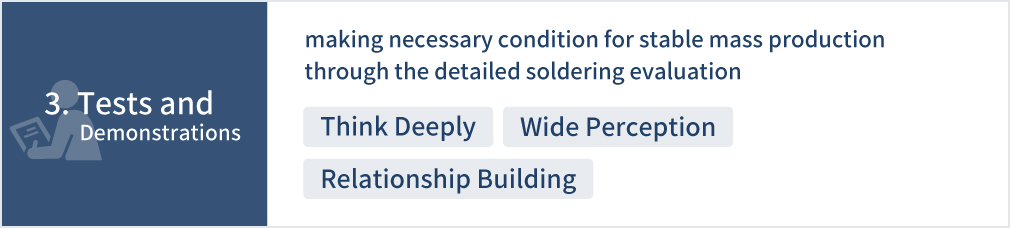
It is important for our customers to establish and maintain a stable mass production system. We identify uncertainties and issues that lie in the production line, and clarify specifications and conditions for solutions. Japan Unix’s testing and demonstrations are conducted for this purpose.
It is our soldering experts who face the workpieces (samples) prepared by the customer and find the optimal soldering conditions. Our engineers, who possess knowledge of metallurgy, fluid mechanics, chemistry, thermodynamics, and mechanical engineering for robot operation, as well as operational management skills from actual production sites, conduct multifaceted testing to find the “optimal soldering conditions”.
For more information about our testing and demonstration, please click here.
4. Specification Matching
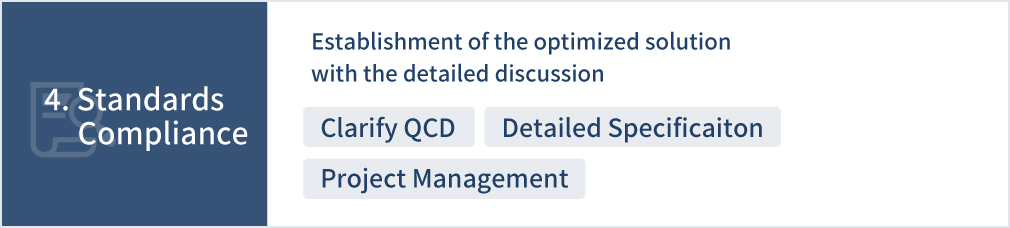
Based on the results of the testing and demonstration, we will propose specifications. However, the important thing is to determine the specifications in a way that is most satisfactory to the customer. What can we do to improve the quality, cycle time, quality, cost, and delivery time required by the customer? Our sales staff, engineers, and customers work closely together to carefully refine the specifications through in-depth discussions. Depending on the project, this is an arduous process that can take up to a year, but we do not proceed to a contract until we are confident that the customer will be successful in mass production.
5. Contracting

After the specifications are agreed upon and the customer is satisfied, we proceed to the contract stage. This is the real start of the relationship between the customer and Japan Unix. Our goal is not to sell products, but to maintain a stable mass production system for our customers. This is a contract for the implementation of solutions that will continue to improve the customer’s issues over the long term.
6. Manufacturing and Shipping
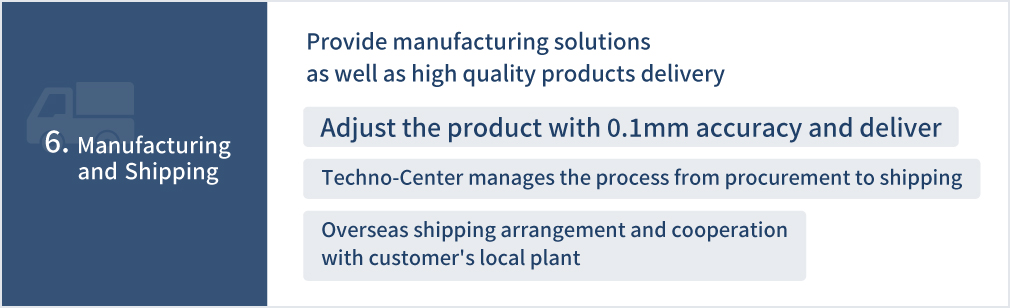
During the period between manufacturing and shipping, we provide project management for the execution phase, including liaison assistance between the customer and the equipment manufacturer of the jigs and safety cover. Products are “Made in Japan” and assembled at the Techno Center, the department in Japan responsible for manufacturing and shipping. Our craftsmanlike staff performs quality control from the procurement stage, making adjustments in increments of 0.1 mm to meet the customer’s specifications. The slightest accumulation of high quality leads to stable quality. We also provide support at this stage, such as post-introduction training for customer operations and necessary paperwork for overseas product shipment procedures.
7. Delivery
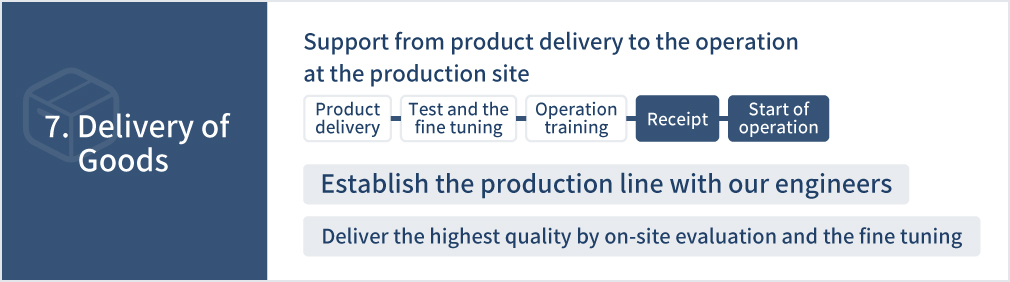
Manufacturing is a delicate process, and different environments have different variables. It is important to be able to derive the targeted conditions under the environment in which the product arrives. To this end, Japan Unix’s dedicated engineers will assist you in starting up on site. In addition to providing operational training for survey staff and on-site workers, we also provide support for local operation, including maintenance methods. In addition to the start-up, we will verify whether mass production is possible without any problems by actually checking the flow of the equipment.
8. After-sales Service

The introduction of a product is not the end of the process. What is important is to keep our customers’ nonstop production. Japan Unix provides full after-sales support to maintain a stable production system, including regular visits and inspections by our sales staff and technical support by our service engineers. For more information on after-sales support, please click here.
Related Information
Related Videos
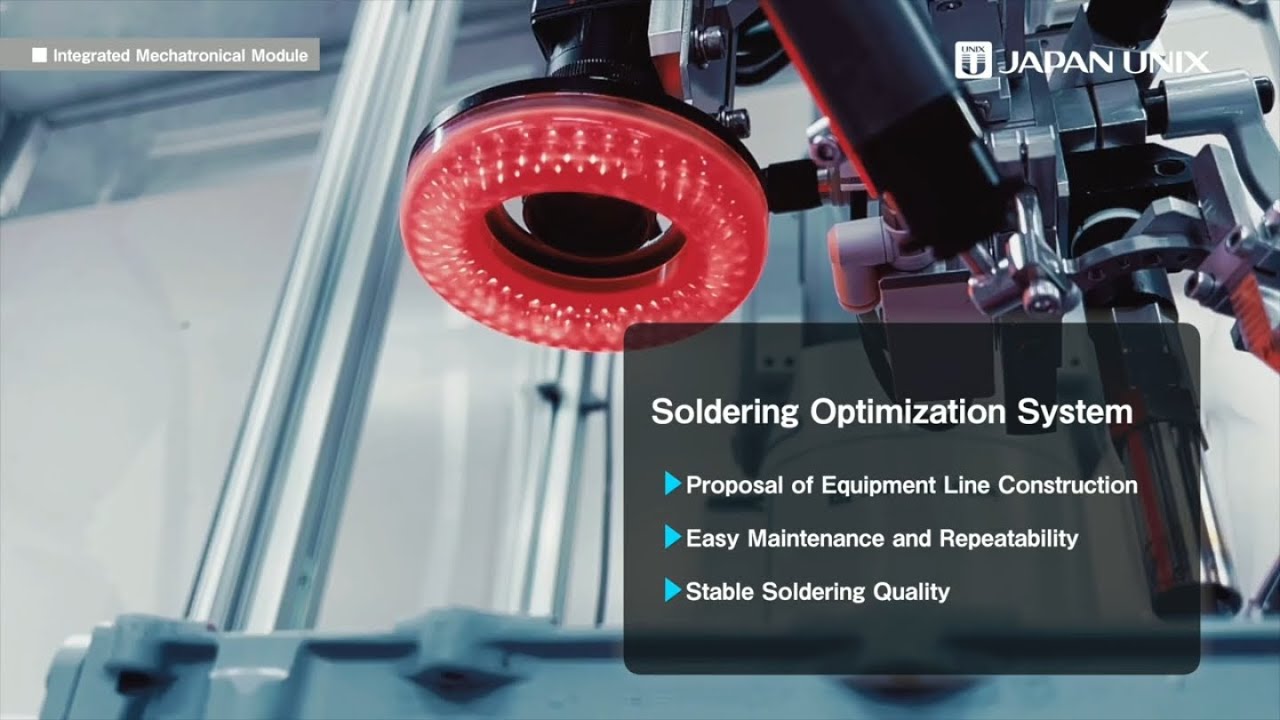