Siemens Japan KK
What is happening in the electrical industry today?
The truth, the depths, and the lifeline
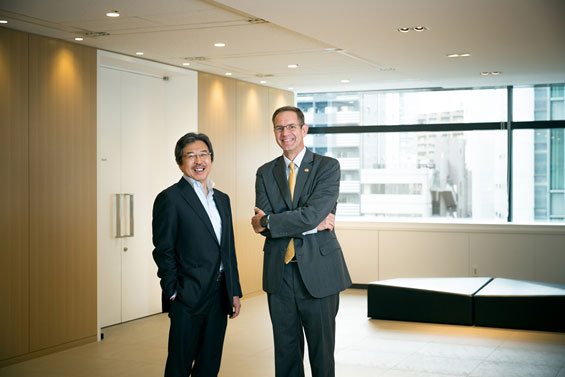
With the rise of emerging economies and the spread of technology changing the shape of manufacturing, what is needed for Japan’s manufacturing industry to compete globally? In this interview, Kenichi Fujita, President and CEO of Siemens Japan, the world’s leading manufacturer, and John W. Mitchell, President and CEO of IPC, which is involved in the formulation and operation of international electronics standards, discuss the “lifeline” of Japanese manufacturers to survive on the world stage.
This article was planned, written and edited by Japan Unix and NewsPicks Brand Design.
To learn more, click here to download the PDF file.
The Fourth Industrial Revolution Caused by Digitalization
What are your impressions of the changes in the environment surrounding the manufacturing industry that are taking place around the world?
Fujita (Siemens): I guess what is characteristic is the digitalization of the entire industry. This has drastically changed the values of the manufacturing industry. Until now, the manufacturing industry’s main value was uniformity of production based on mass production, but with the advent of the digital age, the industry has begun to change to a more individualized and creative workplace.
For example, the sports manufacturer Adidas has begun to introduce a new order and production system that allows consumers to order the sneakers they want, such as “yellow color, rubber sole,” and flexibly respond to their orders.
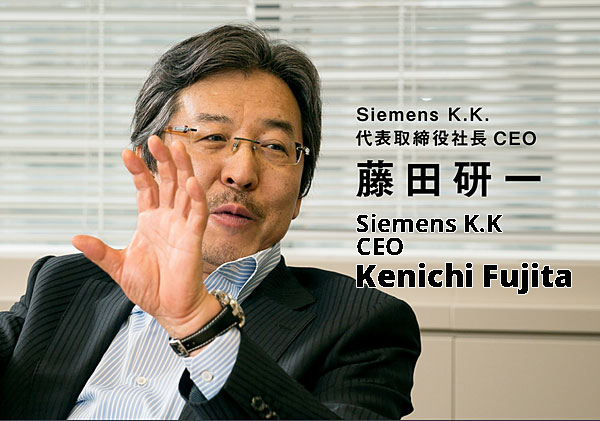
Dr.Mitchell: Yes, that’s right. Sharing is something that is more efficient. Manufacturing is a tried and true process. If this is successful, the amount of data available will increase, and we will be able to make smarter decisions. But this cannot be done without a common platform. This is an area that is just beginning and will have great potential.
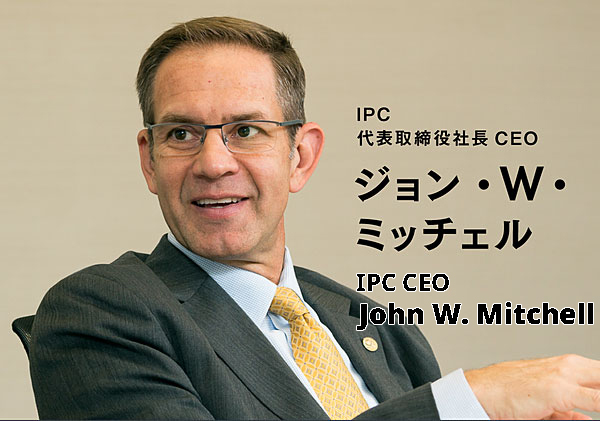
He began his career in engineering at GE Aerospace in 1988 and moved to Alpine in 1992. In 2003, he moved to Bose, where he was the general manager of the New Business Division, Bose’s largest product development strategy. Honor Society, the world’s premier university honor society. D. in Higher Education Management from the Institute of Higher Education at the University of Georgia. He holds an MBA from Pepperdine University and a BS in Electrical Engineering and Computer Engineering from Bryngham Young University. Currently, as head of IPC, he leads the global expansion
Manufacturing, where borders are disappearing
Mr.Fujita: Another key point is that the gap between emerging and developed countries in the manufacturing industry is narrowing.Before digitalization, for example, an order was placed in New Delhi, India. In the past, the local sales company would consolidate the order, which would then be consolidated again at the global headquarters, and then production orders would be sent to the factories in each country and sent to ……, which took a very long time. IoT has changed marketing strategies.
Dr.Mitchell: Just to add a little from an electronics perspective, Japan was the world leader in PCB production from 1989-2005, wasn’t it? The quality of the products was outstanding, and initially costs were kept low. But gradually, the demand for even lower costs led everyone to China. But what about recent years?
According to a survey we conducted last year, the fastest-growing countries are no longer China, but countries like Vietnam and Thailand. Global companies have begun to look to Asian countries where they can produce at lower costs than in China. Vietnam is one of the fastest growing PCB producing countries. And most of the factories producing PCBs in Vietnam are owned by Japanese companies. Thus, as much as 60% of PCB production by Japanese companies is done overseas; in 2016, only 9% of the world’s PCBs were produced in Japan, but Japanese companies still account for 26% of the global PCB market.
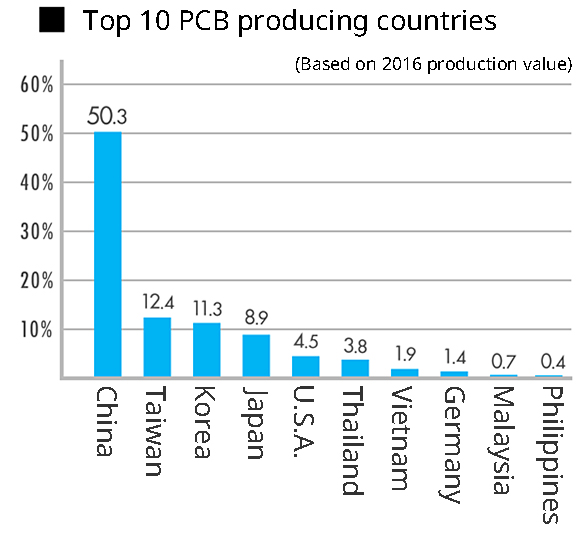
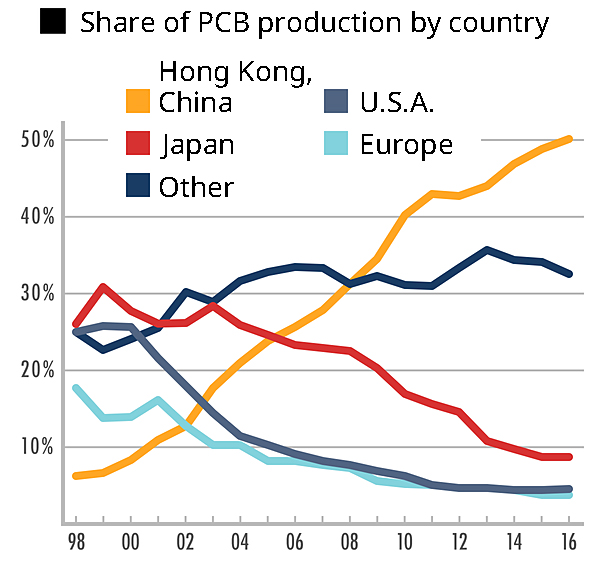
Already 85% of the world’s electronics are IPC compliant
So what is needed for Japan’s manufacturing industry to once again become active in the world?
Dr. Mitchell: IPC is promoting the IPC Standards globally, which are international standards for the electronics industry. Japan will have its own standards. For example, if you go to France and say, “We manufacture to Japanese standard XX,” they will say, “So what?” and even if the quality is actually better than our competitors, they will not understand because they do not know.
The IPC has already been adopted by the electronics industry worldwide. In fact, 85% of the electrical appliances made in the world are manufactured in accordance with IPC. If we can demonstrate this in an international standard, we will be able to understand the global market, which will make it easier to sell our products and greatly expand our business opportunities.
It is not the IPC that determines the standard content. It is companies from all over the world, including Siemens, GE, Boeing, IBM, Bosch, and other companies with significant influence in the global marketplace, as well as smaller companies. In standardization, we always reach consensus. For example, companies such as Samsung and Apple sit at the same table and discuss, but they all have different ways of doing the same job and different opinions. Large companies cannot impose unreasonable demands based on the logic of scale. Because we open our doors to all companies, anyone can make a suggestion if they don’t like something.
Of course, we also provide extensive training programs to ensure that our standards are properly understood and utilized.In Japan, we have launched the world’s first online training program in collaboration with Japan Unix, a leading global manufacturer of soldering robots. The multi-device system makes it easy to learn international standards = global common sense at any time during your commute, lunch hour, or any other gap in your schedule.To be flexible and fast in the global market, we need to invest in technology, but we also need trained personnel who are adaptable.
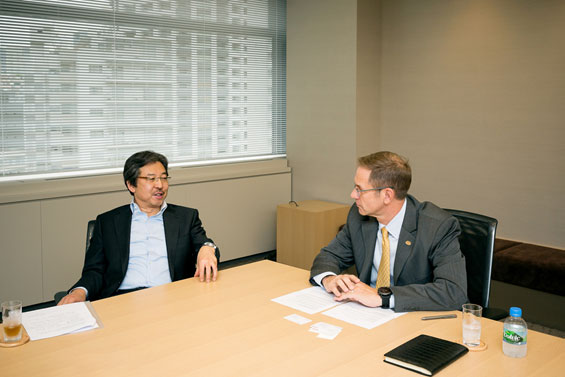
Mr.Fujita: It is very important for companies to develop human resources who can respond to change, not only in the traditional manufacturing industry, but also in the new world we are opening up.
More than half of Siemens’ portfolio has been replaced in the last decade. We must have the management skills to respond quickly to dramatically changing markets and make decisions in an instant. The ability to identify the company’s strong areas and make decisions to leave the weak areas to others. This is what companies will need in order to survive in the future.
Japanese manufacturers have been highly conservative from the production floor. However, they should be more sensitive to risks and opportunities from now on.
To learn more, click here to download the PDF file.