PWB Corporation
IPC Soldering and Rework World Championships
First Japanese World Champion
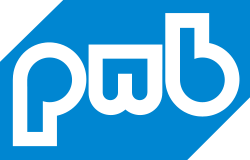
World-class “on-site power” won through daily efforts and accumulation
PWB is where Ryosuke Matsunami, World Champion of the IPC Soldering Rework World Competition 2019, works. Headquartered in Shiga Prefecture, the company focuses on the design and manufacture of printed circuit boards and operates in Japan as well as North America. In this interview, we interviewed him to find out about the world championships he participated in as a world champion and the source of his technical and field skills.
Company Name | PWB Corporation |
---|---|
Founded | Established in 1978, founded in 1982 |
Gross Sales | Private |
Number of employees | 134 (As of February 2019) |
Business | PCB design, manufacturing, mounting assembly and sales, OEM/EMS (contract manufacturing), etc. |
To learn more, click here to download the PDF file.
The result of daily ingenuity and improvement is the first step to world-class performance.

In the midst of the recent negative news in the domestic manufacturing industry, the fact that Japan has proven that it is still at the top level of quality in the world gives great hope and pride to Japanese companies, especially many small and medium-sized enterprises.
The background of winning the world competition was the result of the corporate philosophy of PWB Corporation and the efforts of its employees and Mr. Matsunami, and was inevitable. There is no doubt that the ability to respond onsite to “more difficult production” and “more challenging situations” is the source of the “quality” and “onsite strength” that supports Japanese companies. The daily ingenuity and improvement are the hidden strengths of Japanese companies, and the fact that the accumulation of these strengths matched global standards made them visible to the rest of the world.
10 years of soldering experience. Semiconductor tester substrates that require high quality and precision
Can you tell us about your current responsibilities?
Mr. Matsunami: I am in charge of soldering components to semiconductor tester substrates. Semiconductor tester substrates vary in size, shape, and thickness, and no two are alike. Responding to customer requests leads to trust. I am always trying to find the best way to meet the customer’s needs, and I am always willing to try if I can do it.
Mr. Nishikawa: Our company has originally been engaged in an integrated business for cell phone manufacturers, from artwork design of printed circuit boards to manufacturing, parts procurement, mounting, assembly, and chassis design. in 2000, we entered the semiconductor-related business, developing inspection boards used by semiconductor memory and IC manufacturers. Mats (Matsunami-san) has been in charge of soldering semiconductor tester boards ever since he joined the company.
I was extremely nervous at the Japan competition.
How did you come to participate the Japan competiton?
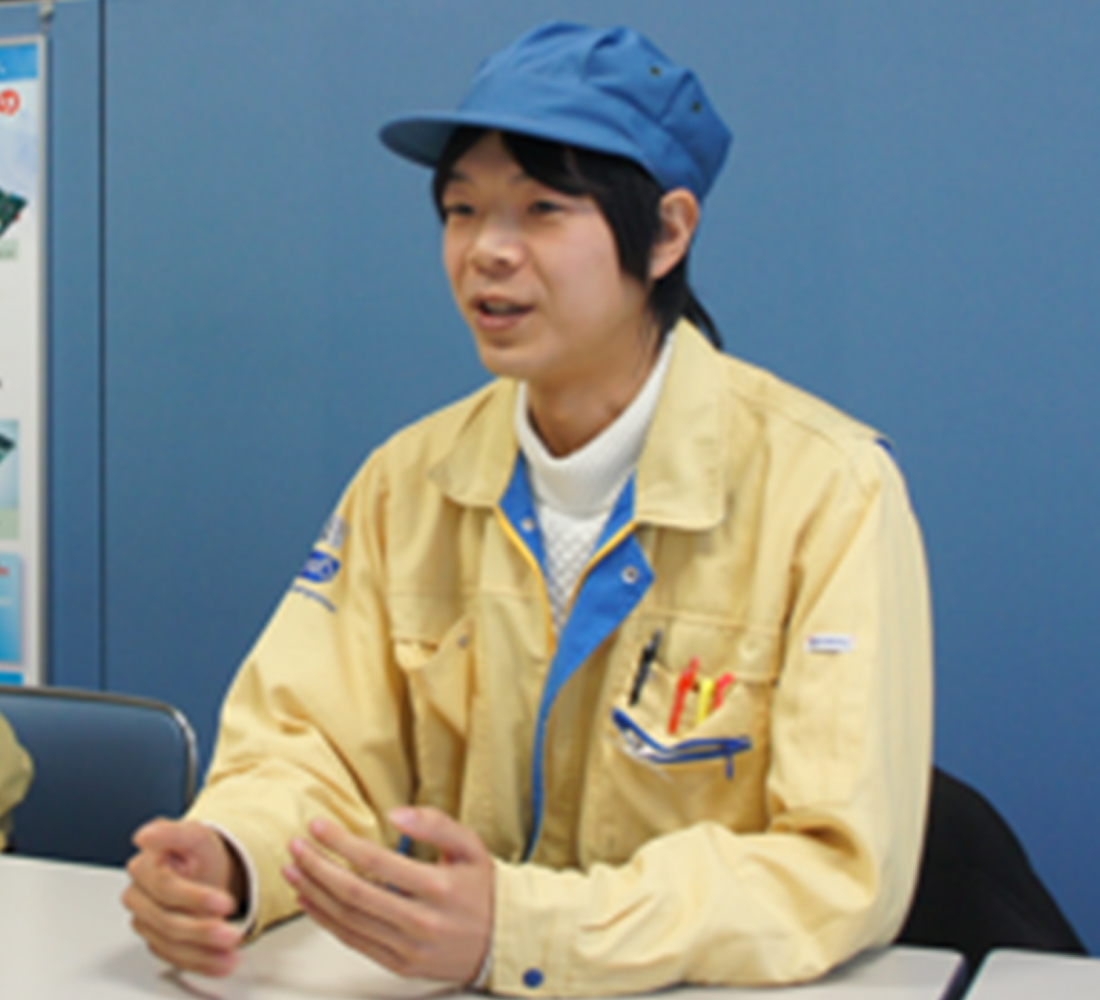
Mr. Matsunami: I solder a variety of boards every day, but I rarely have a chance to see the outside world, and I have always wondered what level I was at. Just then, I received an e-mail from Japan Unix about the IPC soldering contest in Japan and decided to participate.
Mr. Nishikawa: I thought Matsu’s work was very beautifully finished and not poorly done. I thought it was important not to be a frog in a well and to know where my level was and to see and experience many things, so the company pushed me. (Scenes from the Japan Competition)
He was the only one of the participants to complete all the tasks and win the competition!
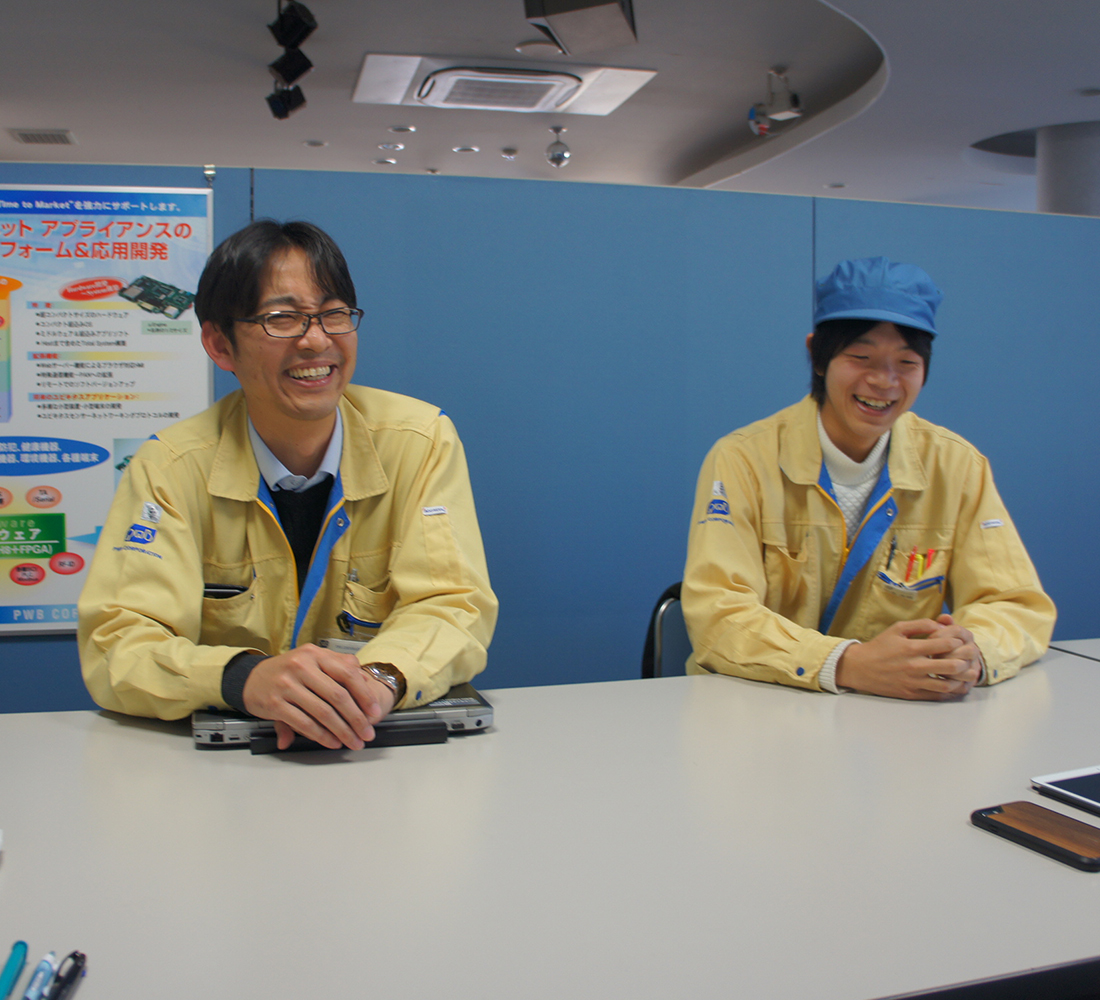
You won the Japan competition and qualified for the World Tournament. How did you spend your time during this period?
Mr. Matsunami: I returned to my normal work, but I felt that the bar had been raised one more notch, with salespeople doing PR for their clients and customers expecting higher quality from us. I am now more conscious of the finished product than before.
While soldering was the only task for the Japan competition, rework, which involves removing and re-mounting components, was included in the world competition. I attended training for this purpose at an IPC-accredited training center in Tokyo for about four days. Until now, I had done soldering and rework on my own, but it was very beneficial to learn theoretically at IPC, which is the industry standard. I discovered many things I didn’t know and many areas that differed from my own methods, and the training here helped me a lot in the real world.
It’s time to go to the U.S. Local staff will provide full support. Unexpected happenings at the competition
How was the competition? You had representatives from countries all over the world, and this time you had soldering and rework.
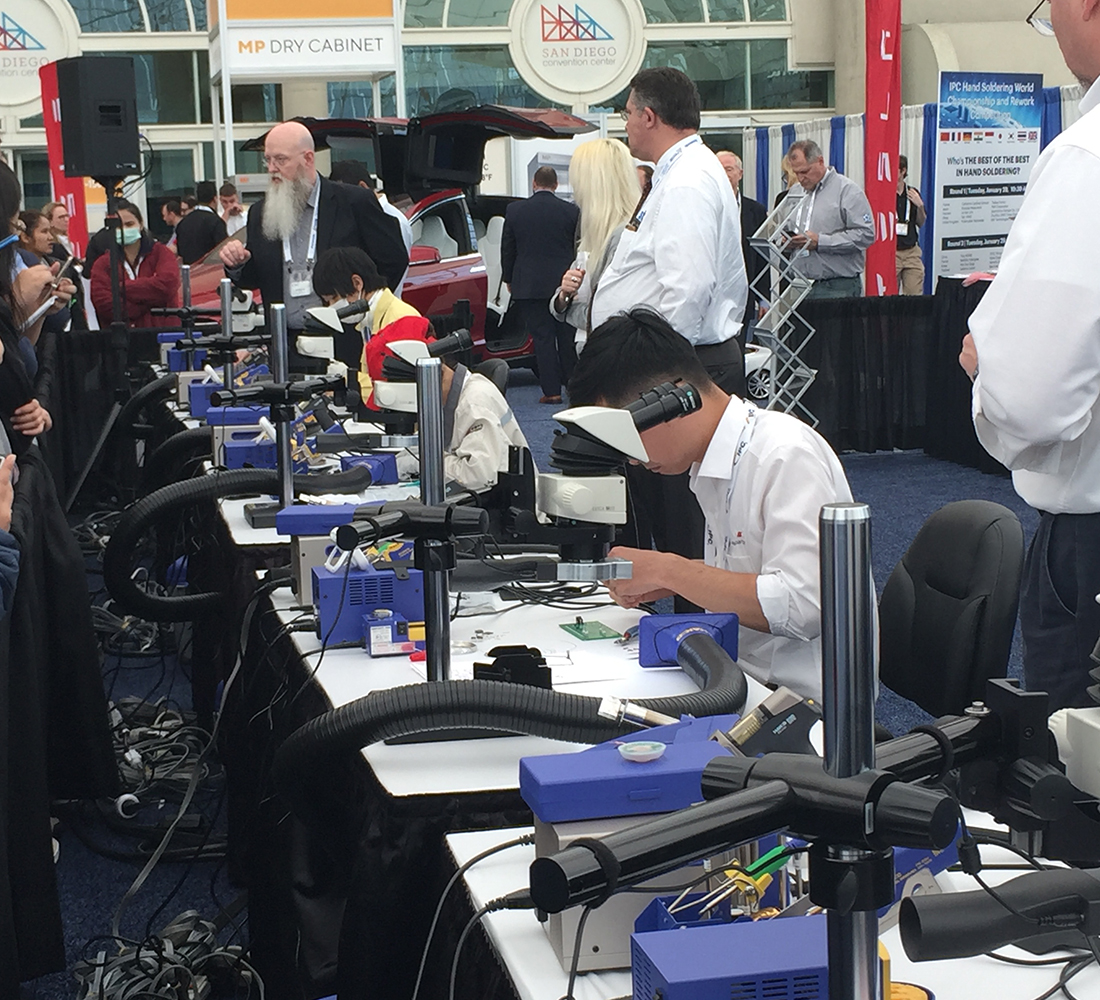
Mr. Matsunami: The event took place over two days, and I arrived there the day before the convention. The staffs from our local subsidiary, PWB America, Inc. joined us and supported us in everything from transportation to accommodations and meals. Thanks to them, I was more relaxed than in Japan. I had heard in advance that people in China and other countries are considerably faster in speed. But this time, rework was on the agenda, and it was clear that speed was to be evaluated when quality was tied, so I knew from the start that careful work and quality were important. When it came to the world competition, it was a matter of course to complete the work, and then I tried to do each task carefully and meticulously while thinking about it.
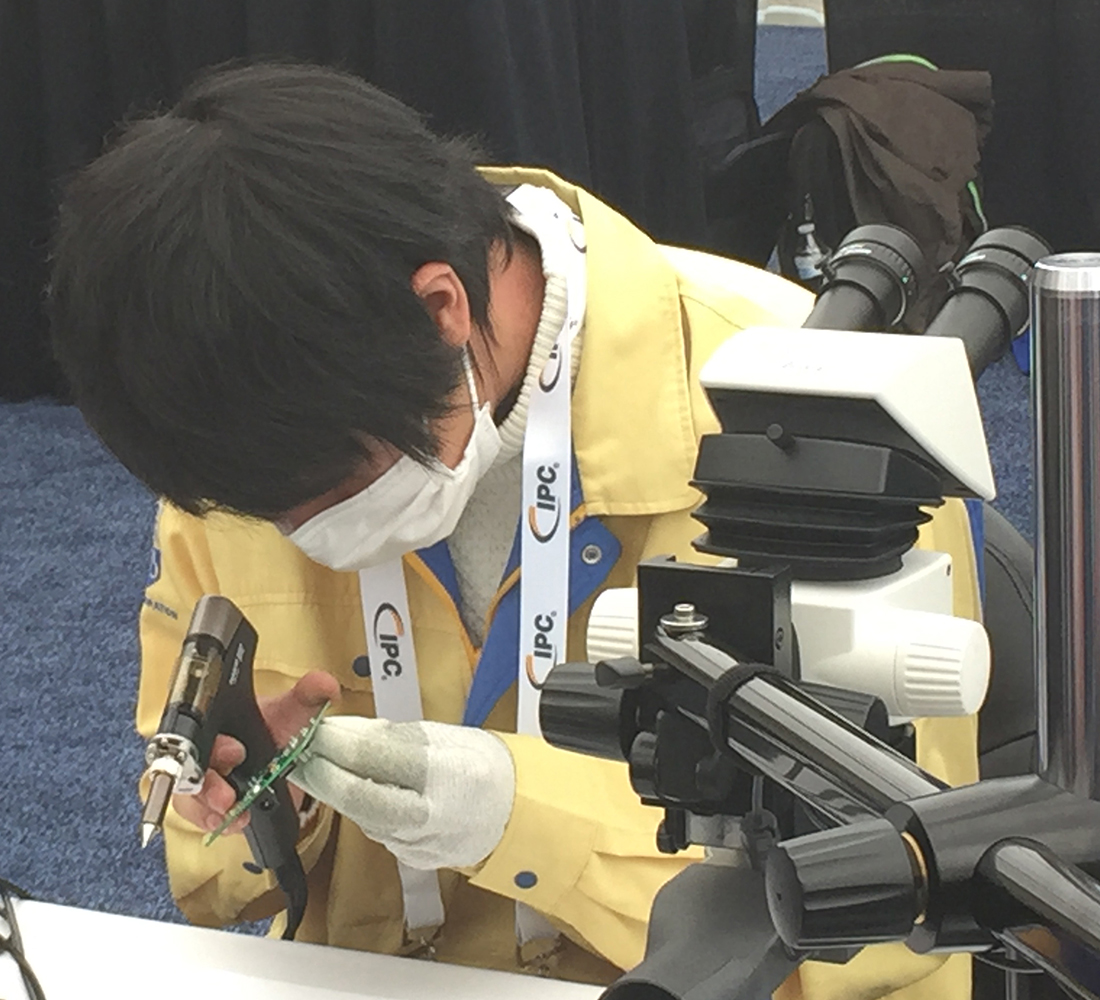
Mr. Nishikawa: Matsu’s work is by no means slow. It is just that compared to other participants, he was able to finish the assignment within the time frame, which is quite fast. And yet the work was meticulous. I think they were balanced at a high level.
Mr. Matsunami: My impression of the participants from other countries was that they were indeed fast in their work, but a bit pushy was noticeable. In particular, I got the impression that they lacked carefulness when removing parts for rework. There are many mass production factories in China and Southeast Asia, and I wondered if many of them were working there.
I had some trouble at the convention.
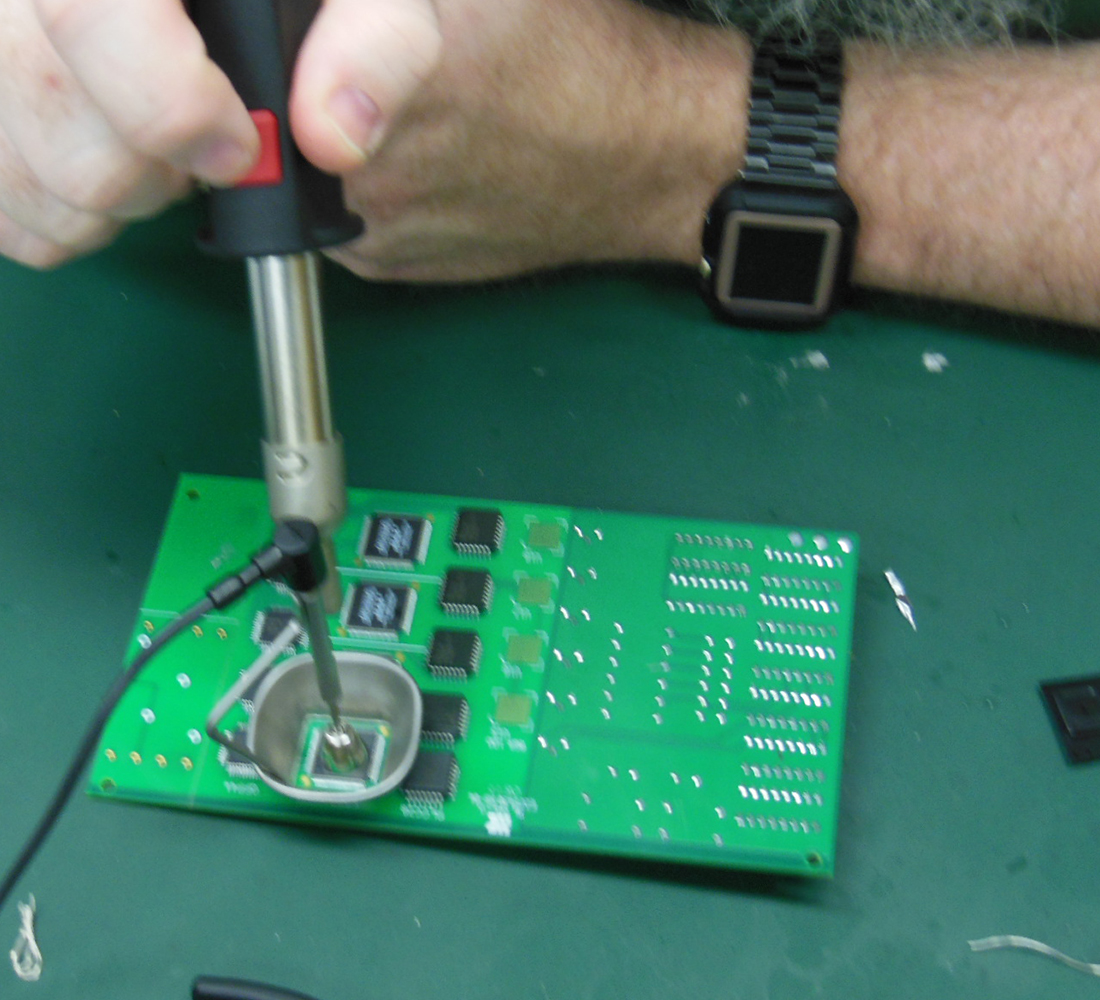
Mr. Matsunami: Due to an inadequacy on the part of the tournament management, the flux was not prepared.(laughs). So just before the tournament started, it was decided to conduct the event without flux this time. While using flux is routine, the level of difficulty increased dramatically.
Mr. Nishikawa: I was really surprised at Matsu after the unexpected happened. regarding the reworking of QFP, normally we use flux and apply warm air to remove the QFP. This time, however, there was no flux. So he wrapped solder around all the joints and removed the components while taking advantage of the flux in the solder. Then he cleaned the pads and mounted them again. Matsu was the only one who did it this way. The other participants struggled with applying warm air and forcing it off. That method damages the pad and is not the right choice in that situation.
[The method applied by Mr. Matsunami: solder wrap method.
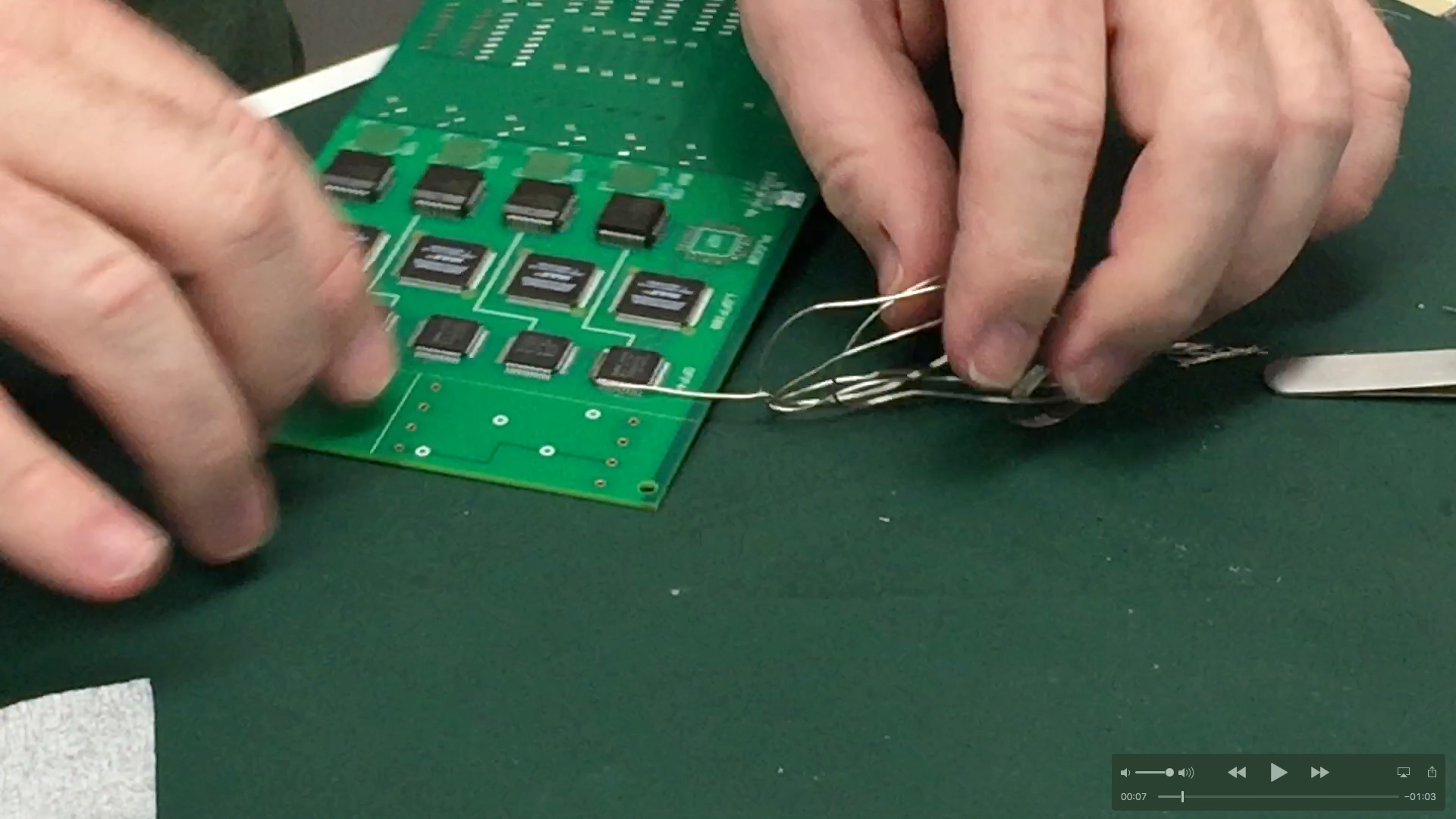
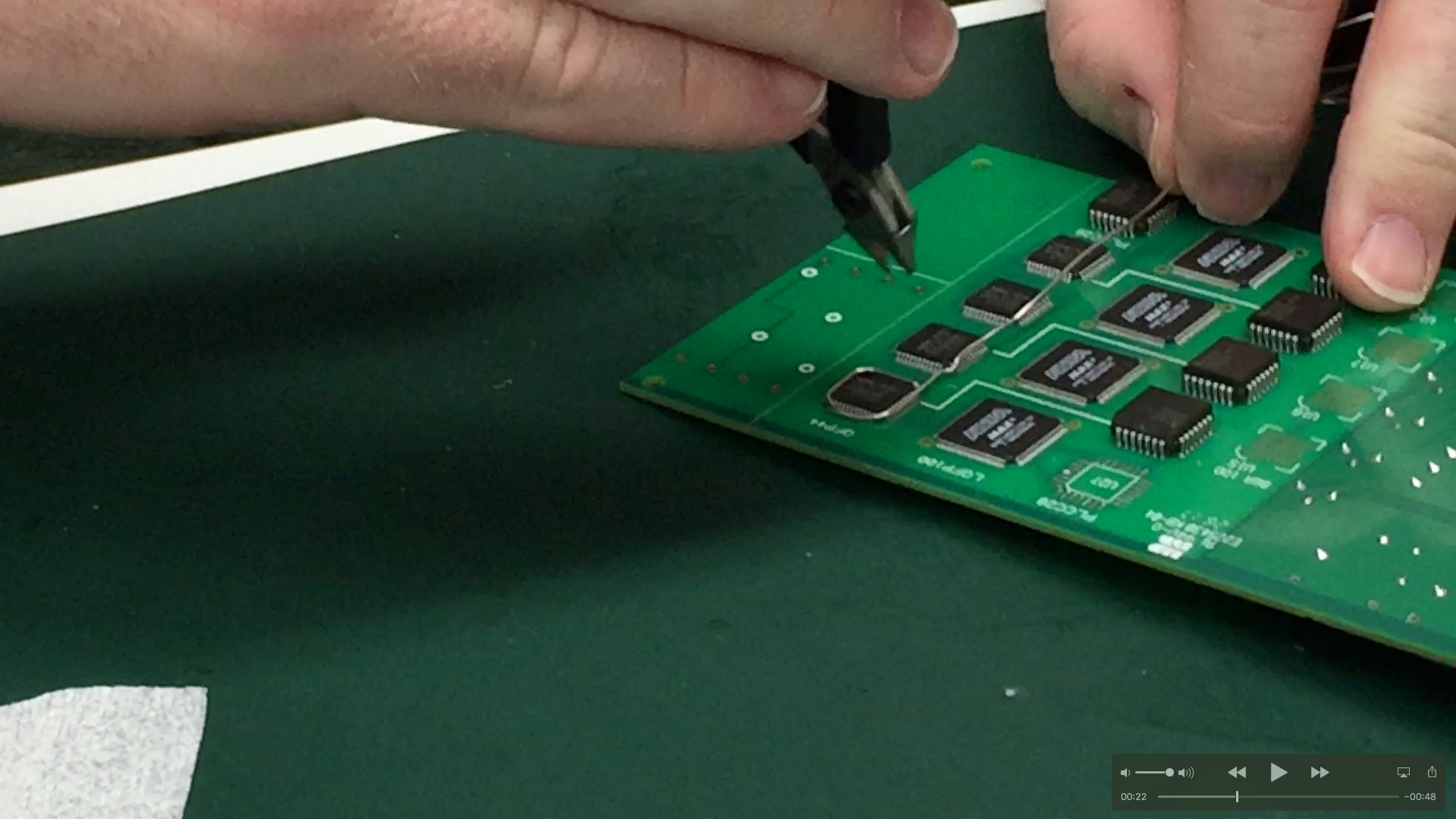
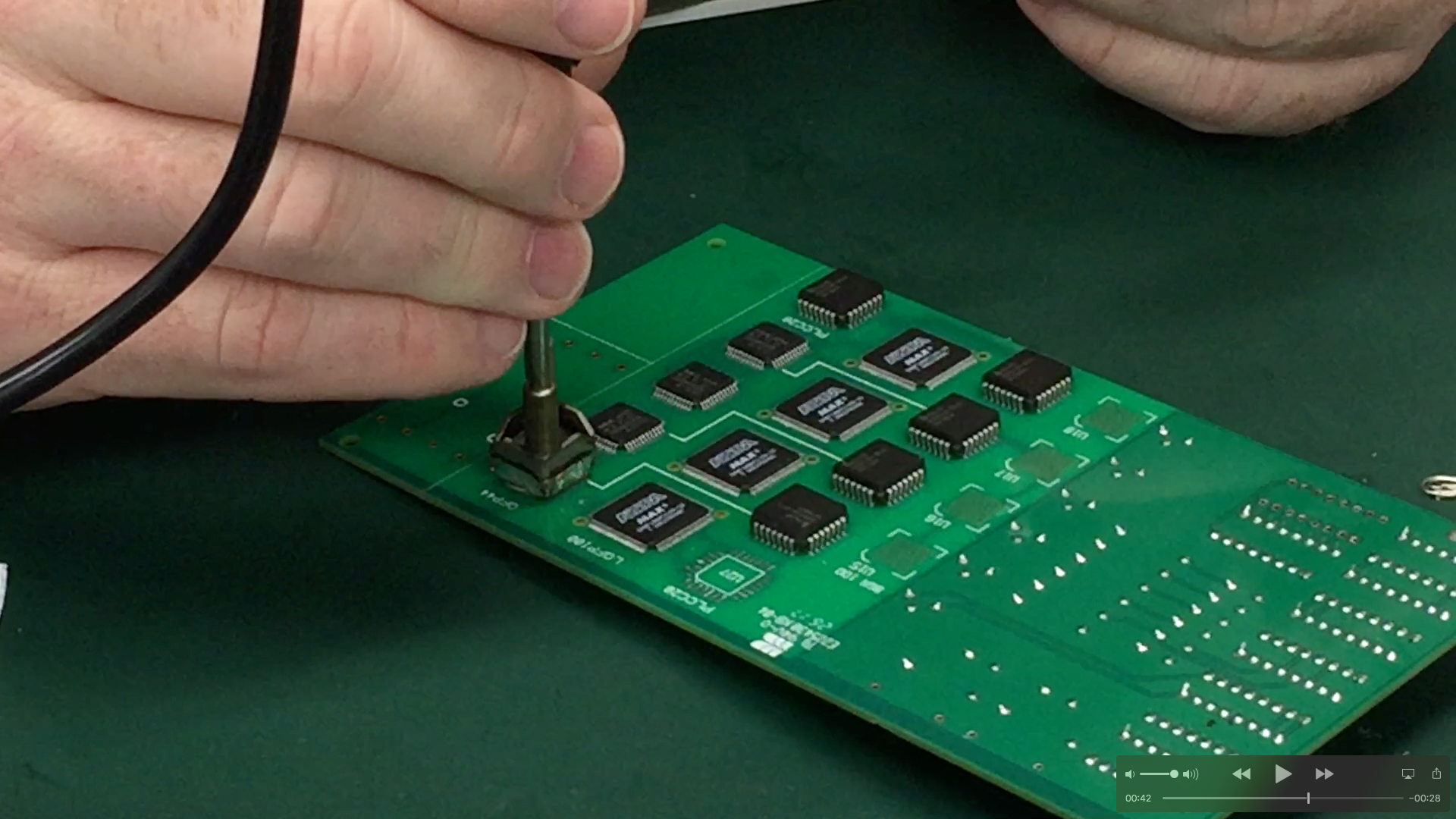
*Wrap thread solder around the QFP and remove it with a soldering iron (IPC-7711/21 Section 3.7.2.1)
Mr. Matsunami: I also applied warm air at first but could not remove it, so I changed to this method. It reduces the speed, but after removal, the pad is restored to its original state, and subsequent re-mounting can be done cleanly. I was also taught this method in training after the Japan competition, so I was able to take advantage of it. I was surprised when I was told there was no flux, but I think the fact that I was able to move quickly in that situation was a result of my training.
Mr. Nishikawa: I was impressed by your resourcefulness. Perhaps it was my experience in dealing with day-to-day problems that helped. Our company culture is to “always think of a solution and do something about it,” even when we are backed into a corner. I believe that the addition of Matsu’s never-run-away attitude created a good synergistic effect.Scenes from the World Convention (YouTube)
As a result, you won with a perfect score for the first time in history, becoming the first Japanese to win the world championship.
It is the first time in history that you won with a perfect score. Were you aiming to be the best in the world from the beginning?
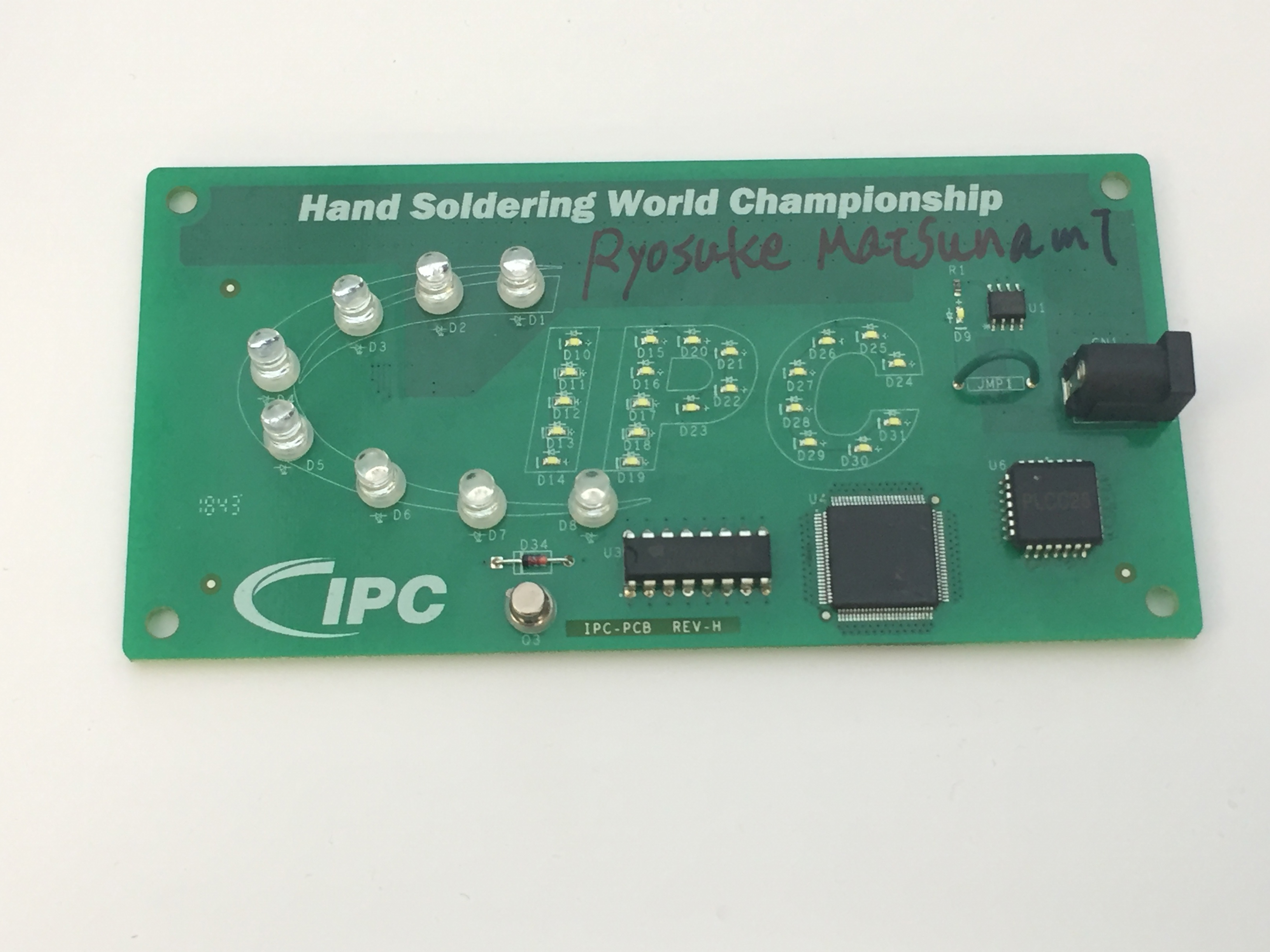
Mr. Matsunami: I was half aiming to become the world’s No. 1 and half feeling a bit weak. I was also enthusiastic that I could contribute to the company and expand the company’s name by doing my best in these situations and becoming the best in the world. On the other hand, there was a part of me that thought that I could learn a lot just by watching other participants’ work methods.
How did you feel when you won?
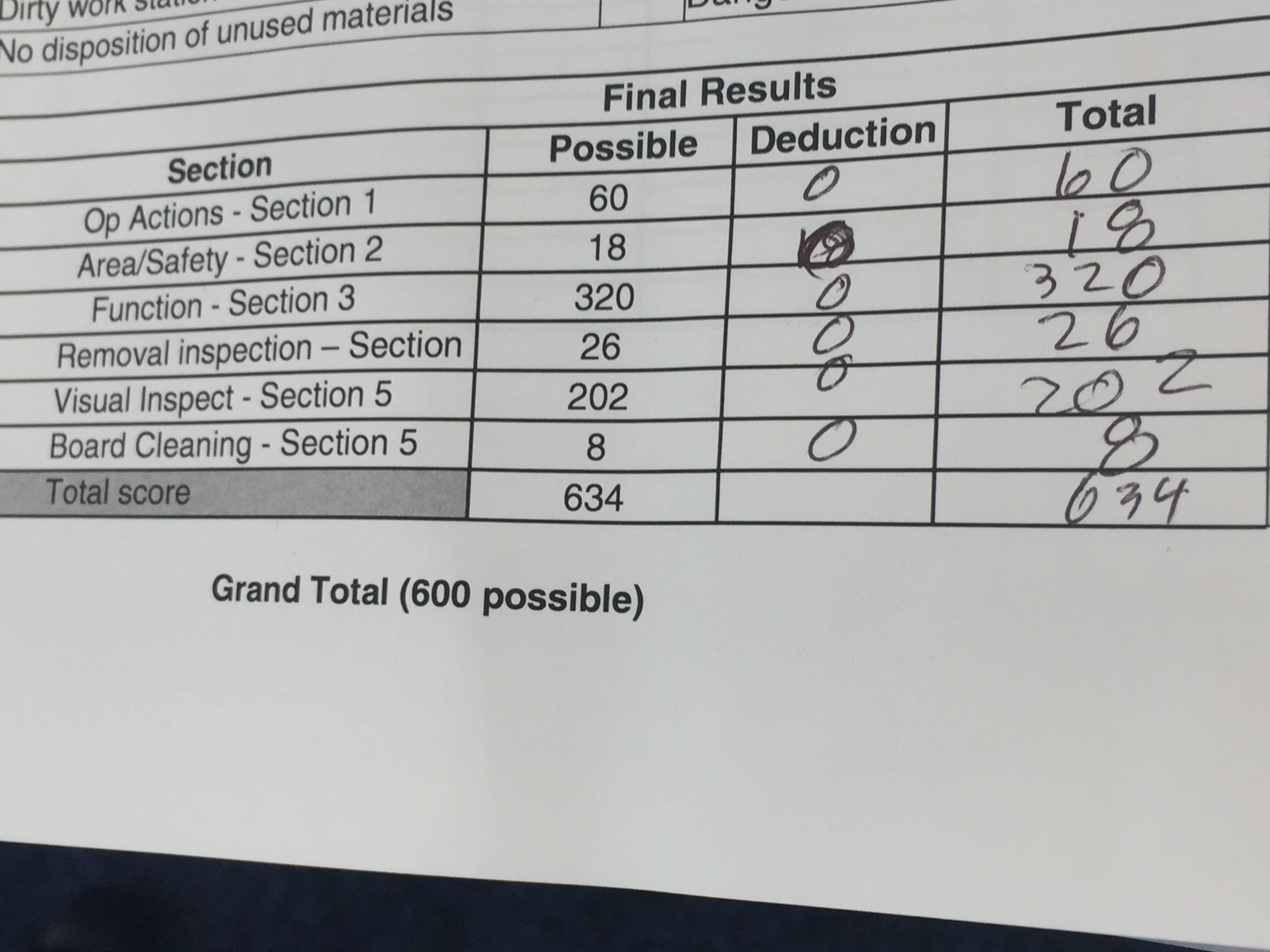
Mr. Matsunami: I remember that when the announcement was made, Mr. Nishi and the local attendants were very excited. I was most happy that I had done what I could do and that the people around me were happy about it.
Mr. Nishikawa: The chairman, the founder of our company, was really pleased. He was really happy that such a wonderful engineer was born from the company he founded and achieved results in the world.
Mr. Matsunami: I was very happy that the chairman, president, and everyone in the company were so pleased. After returning to Japan, they held a victory celebration party at the hotel, and dozens of people came to the party. The best thing is for the company to be excited, so I was really happy in that sense.
My goal is to become a professional soldering engineer. I want to spread the joy of soldering.
You are the best in the world. Do you have any goals or things you want to do in the future?
Mr. Matsunami: The company, including the president and Mr. Nishi, always tells its employees to “become professionals. A professional is someone who has mastered both technique and theory and can verbalize them. I am confident in my skills because I have experience and my body remembers them. I am still learning the theory, and it is still a long way off from being able to teach it to others. Still, in the future, I would like to become a soldering expert and be in a position like an instructor or teacher, and convey the joy of soldering to children and many other people.
I have been constantly thinking and working for all 10 years and made many mistakes, but how to make the most of them. That is why I enjoyed IPC training because I was able to acquire new knowledge and skills. It is a repetition of how to apply this to the next work and devise new ways of doing things.
Mr. Nishikawa: As a company, we would like to think of ways to make the most of Matsu’s technology and achievements. After the World Convention, I was taken to a company in the U.S. that specializes in business to rework for the aviation and space industry. Although they have a limited number of clients and the number of projects is not large, it was very interesting to see that they require a high level of technology and there is a constant need for it. I sometimes wonder if it would be possible to develop such a business in Japan, for example.
Mr. Matsunami: That sounds interesting.
Finally, as World Champion, what are your plans for the next and subsequent tournaments?
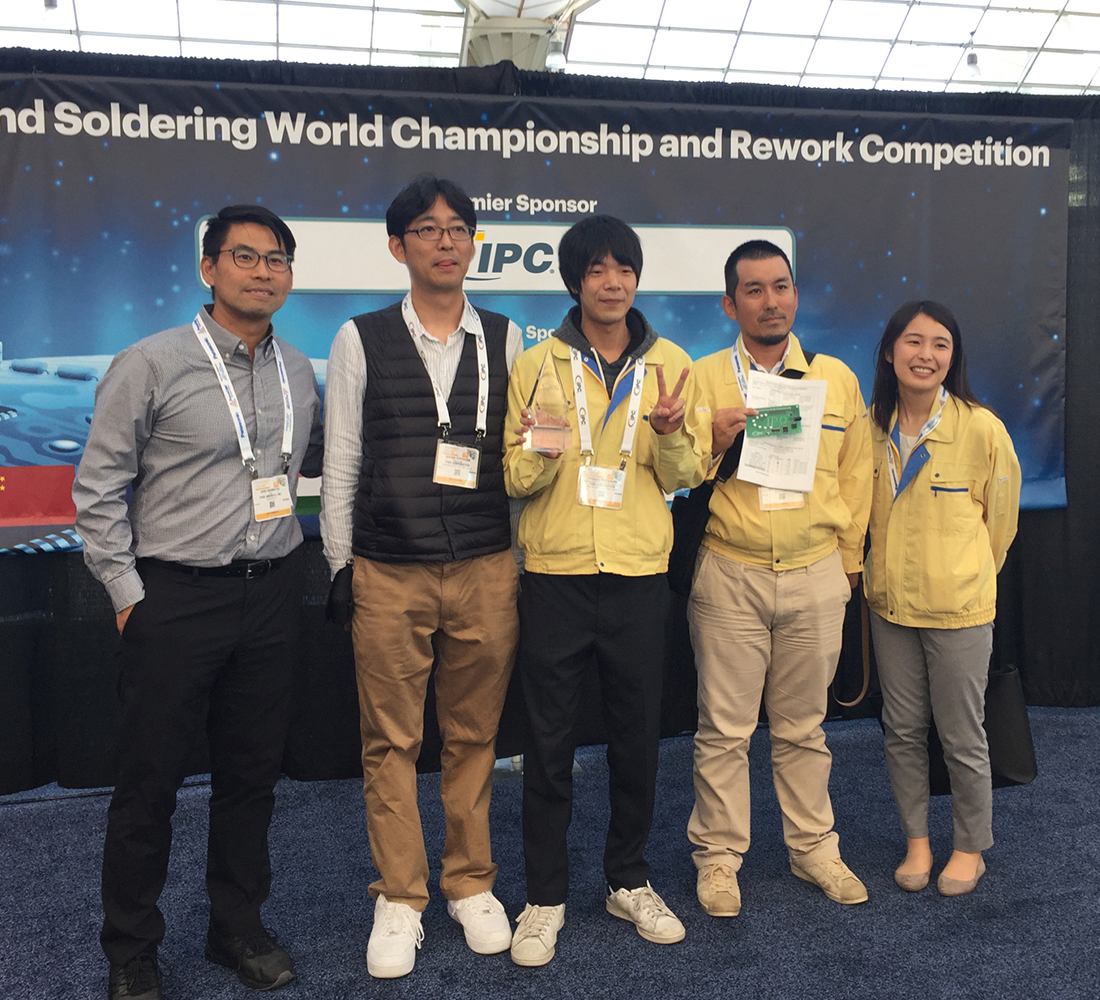
Mr. Matsunami: I have heard from IPC that there will be more participants in the next competition in Japan because of the buzz around this year’s event. I am sure that there are many excellent engineers in companies in Japan, and I am interested in competing with them. If given the chance, I would like to do it again. Soldering technology is changing, and the competition is a great opportunity to learn and experience it. However, the winner is not eligible to participate in the next competition. So next time, I would like to have someone else compete and I will be able to support them well (laughs).
Editor’s postscript
At IPC, soldering alone, as it used to be, is not likely to make such a big difference in a world competition, and it becomes a speed competition. Quality is essentially the first priority, and speed is not the objective. For this reason, we have increased the difficulty level by adding rework, which requires more technical skills this time.
Although soldering and rework are limited to the world of soldering and rework, many Japanese companies must have latent strengths that can be used globally, just as PWB does. We hope that as many companies as possible will demonstrate their strengths to the world and link them to the electronics industry and the global market, where high-densification is progressing.
To learn more, click here to download the PDF file.