NSK Ltd.
Adopted for automotive parts manufacturing and realized the effects.
The key to reducing production costs and stabilizing quality is the combination of global standards and in-house standards!
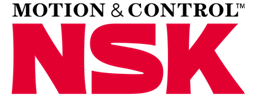
NSK is a long-established top manufacturer of bearings used by major domestic and overseas manufacturers. We spoke with the Design & Quality Control Department of the Automotive Parts Division about the process and effects of the introduction of IPC.
Company Name | NSK Ltd. |
---|---|
Founded | November 8th, 1916 |
Gross Sales | 974.9 billion yen(FY2015) |
Number of employees | 974.9 billion yen(FY2015) |
Business | Founded in 1916 as a pioneer in manufacturing Japan’s first bearings. Since then, the company has been the number one manufacturer in Japan and one of the leading companies in the world. Using the precision processing technology cultivated in the production of bearings, the company has successfully diversified into automotive parts, precision machinery products, and electronic application products.In the 1960s, the company began full-scale global expansion, opening new production and sales bases in Brazil in 1970 and in North, Central, and South America, Europe, and Asia in the following years. Particularly in the rapidly growing Chinese market, the company has built a solid structure that enables it to be self-sufficient in everything from R&D to sales and technical services. |
To learn more, click here to download the PDF file.
Differences from IEC and JIS. Decided to adopt it in conjunction with our own standards.
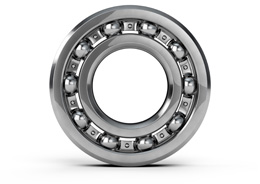
How did you come to introduce IPC?
In the early 1990s, when we spoke with suppliers in China and Taiwan, “IPC” came up frequently from them. Knowing that suppliers in Asian countries were instructed by the Western manufacturers from whom they placed orders to manufacture in accordance with IPC, we decided to adopt IPC in conjunction with our own standards, judging that information on IPC was indispensable for our global expansion. The contents of the IPC are also stipulated more broadly, finely, and deeply than those of the IEC and JIS, while also working closely with the IEC, which is an international standard.
IPC is responsible for storing the entire product.
Customized for the field and uniform quality even across multiple countries.
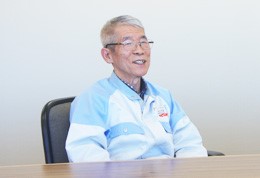
Design & Quality Control Department
Mr. Toshiyasu Takei
What standards were you manufacturing to before that?
We were proceeding within JIS, the standards of each supplier and client, and our own quality standards. However, JIS defines the minimum standards to be followed, but does not cover everything. The same is true for the specifications of clients, which vary in style and level. Overseas, the ordering side requires that the IPC be adopted as a condition for placing an order, and the side that receives the order, such as EMS, must also comply with this.
How do you utilize IPC?
The manufacturing standards are only as good as the quality demanded by the customer. Especially for automotive manufacturers, who have high quality requirements, IEC and JIS are used, and IPC is used for the areas not specified in those standards. In practice, there are many cases in which it is difficult to understand or judge even by looking at JIS or IEC. The IPC is used as a solution in such cases.
For each operator working on the shopfloor, IPC’s quality conditions are customized for the actual shopfloor. We have created an “instruction manual” that describes the judgment of good and bad products for each process using actual products. By reconstructing the actual site and products, various operators can work in accordance with the IPC, and quality can be standardized across many countires.
Significant cost reduction and quality stabilization.
Start with internationally recognized standards and gradually establish your own standards.
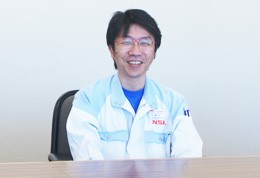
Automotive Components Division
Mr. Koichi Sato
What are the benefits and positive aspects of using IPC?
By aligning quality standards, which had been difficult to standardize in our company, with IPC, judgment criteria became clearer and the defect rate due to quality variations was reduced. In addition, the production staff and quality inspectors are now able to have the same standards of judgment, making communication easier.
On the other hand, IPC covers many areas, but based on its own product specifications, the processes necessary for quality improvement are defined as its own standards. Translating in-house standards into multiple languages and deploying them in other countries requires a great deal of effort and cost. By adopting IPC, which has already been translated extensively, we were able to achieve significant cost reductions and quality stabilization at the same time.
The moment you step out into the world, IPC becomes indispensable.Expanding the quality standards of the mother factory in Japan to other parts of the world.
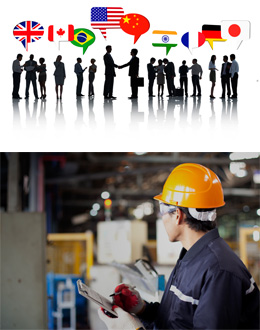
How about the benefits for global business?
The IPC has been translated into many languages, including Spanish, Chinese and Thai, as well as Japanese and English, and has been very helpful in extending IPC-based Japanese mother factory practices and quality standards to other factories around the world.
When doing business in Japan, JIS will suffice. When you expand your business globally, you are always faced with IPC. Also, when entering a new business, it is sometimes difficult to determine to what extent quality standards should be set. In such cases, it is possible to start with internationally recognized quality standards based on IPC and gradually establish your own standards to improve quality.
Advice for companies considering IPC
The IPC is very easy to understand, with detailed explanations of the work with pictures and images. It is like a textbook or reference book. If we use it as a standard and utilize it for our own use, we will be able to give precise instructions to our operators. IPC is also important for building relationships with overseas manufacturers; it has a positive effect on many aspects, including manufacturing efficiency, quality uniformity, and business expansion. I hope you will make good use of it.
To learn more, click here to download the PDF file.