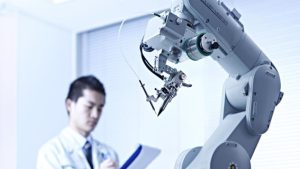
What is a soldering robot? What are the benefits and future challenges of automation?
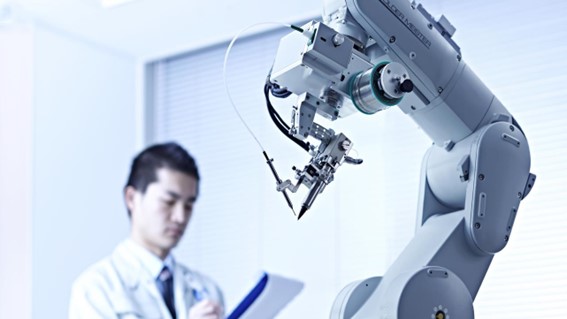
What is a soldering robot? The benefits and future challenges of automation.
Table of Contents
- Soldering Robots Automate Soldering Operations
- Difference between automated soldering equipment and soldering robots
- Advantages of soldering robots
- Challenges with soldering robots
- History of soldering robots
- Current soldering robots
- Future requirements for soldering robots
- Continuous evolution of soldering robots
Soldering Robot for Automated Soldering Work
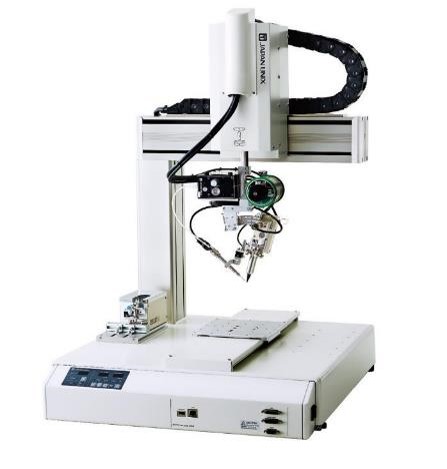
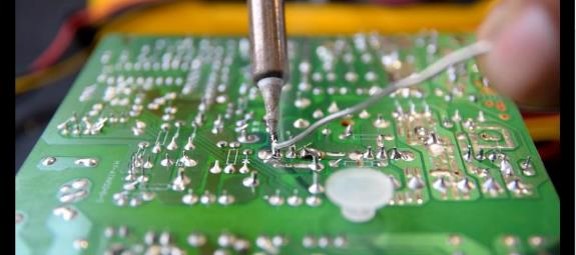
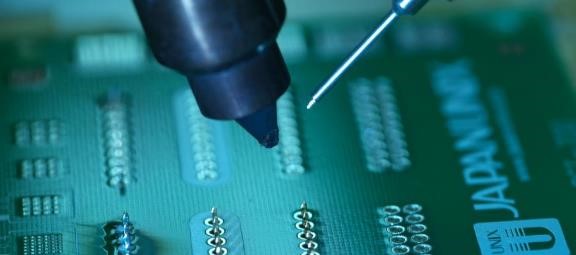
The first appearance of soldering robots can be traced back to the 1970s when industrial robots such as those used in automobile assembly, welding, and painting were introduced, establishing the category of industrial robots. Initially, these robots had a soldering iron attached to the end of their arm, but their precision was not sufficient at that time. Even after the introduction of soldering robots, soldering remained primarily a skilled craftsmanship performed by experienced workers.
However, with technological advancements, the precision of soldering robots has improved. In addition, the transition to lead-free soldering since the 2000s has increased the difficulty of soldering. Furthermore, factors such as the increasing complexity of circuit board designs, labor shortages, and the challenge of knowledge transfer have contributed to the widespread adoption of soldering robots.
The significant difference between humans and robots lies in the time required to master the skills. Skilled human soldering operators can make fine adjustments based on their senses, making them suitable for soldering delicate components. However, achieving that level of skill requires a considerable amount of training over a certain period of time.
Modern robots, on the other hand, can start operating immediately after initial setup and are capable of soldering at a higher speed than humans from the day of their introduction.
Differences between Automated Soldering Equipment and Soldering Robots
There are two main methods for automating soldering: “automated soldering equipment,” which efficiently performs soldering in batches, and “soldering robots,” which perform precise and detailed soldering. Each has its strengths and weaknesses, so they are used selectively in production lines according to specific requirements.
Automated Soldering Equipment
Both methods are used when efficient soldering of electronic components onto a circuit board in bulk is desired. However, the flow method is not suitable for fine soldering in densely packed areas, while the reflow method cannot be used for soldering heat-sensitive components.
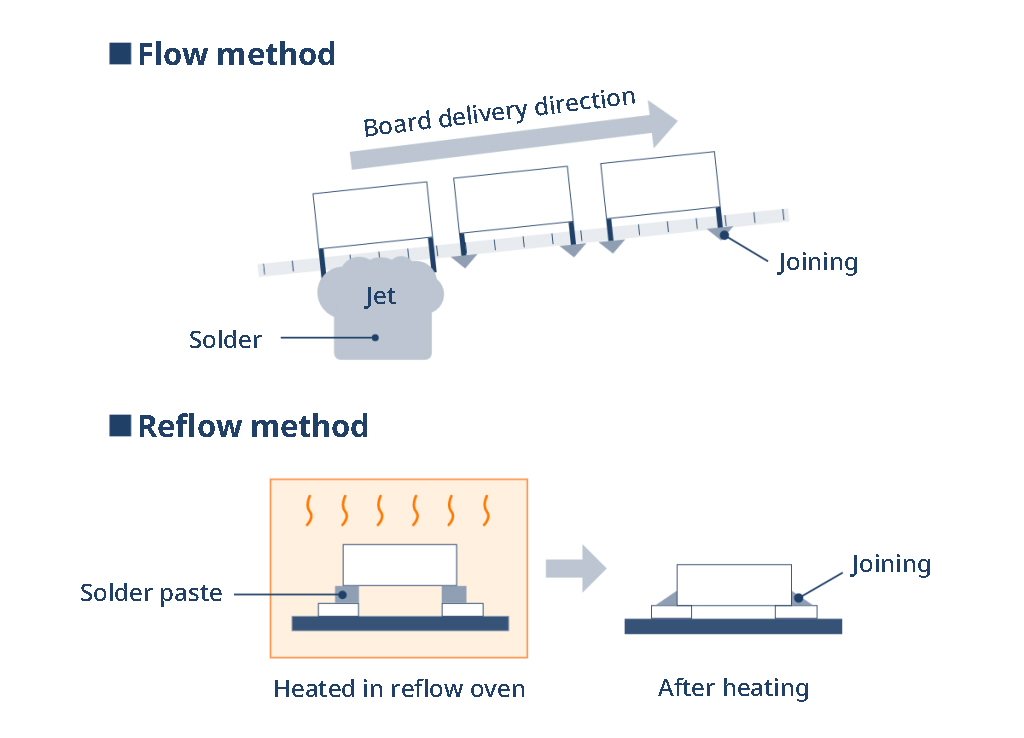
Soldering Robots
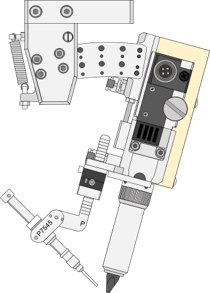
Advantages of Soldering Robots
For example, in the case of Japan Unix’s soldering robots, the soldering position is adjusted with a correction accuracy of ±0.05mm using a soldering iron tip position correction mechanism, ensuring high reproducibility. Furthermore, by setting optimal conditions for up to 255 items, such as solder feed rate, speed, and approach for raising and lowering, they achieve stability in soldering quality.
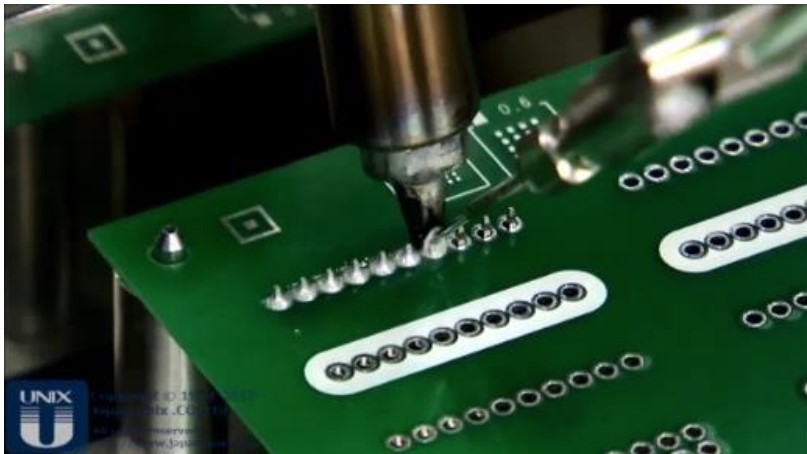
By introducing
soldering robots, soldering can be performed with high speed and accuracy compared to when the same task is carried out by humans, which is the advantage of using soldering robots.
Challenges for Soldering Robots
For these types of soldering tasks, skilled human operators are more suitable, and currently, not all soldering work can be replaced by robots. While there have been significant advancements in technology, it still takes time to fully replicate the skills of skilled human workers.
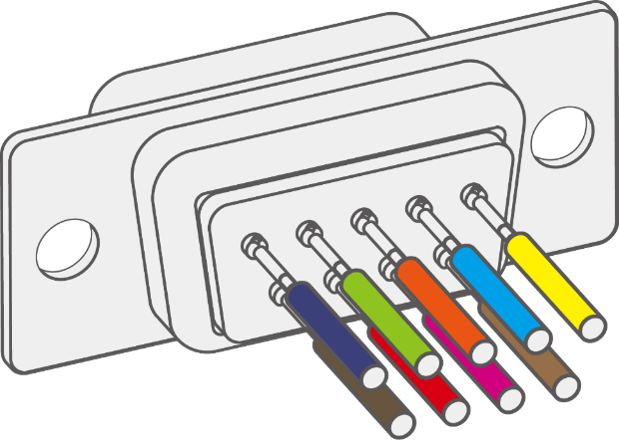
History of Soldering Robots
Japan Unix, in collaboration with an automatic machine manufacturer, developed the first soldering robot that aimed to replicate “human hand movements” in the early 1980s. By 1983, they began supplying full-fledged soldering robots.
In 1985, the vertical multiple-joint 5-axis soldering robot “UNIX-511” was completed. Since then, research and development have been ongoing to improve performance, including repeatability, operation speed, and external input/output capabilities, leading to the present day.
Previously, soldering robots were considered as a “replacement for simple tasks performed by humans,” but with a decline in skilled soldering workers, the user needs have shifted to “using robots to handle tasks that are difficult for humans.”
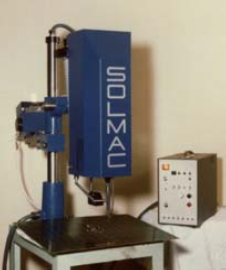
Types of Soldering Robots Based on Structure
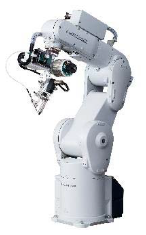
“Vertical multi-joint type (5-axis, 6-axis)”
A versatile type capable of handling three-dimensional work
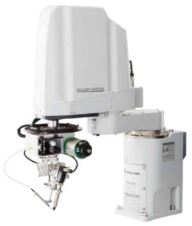
“Cylindrical coordinate type (scalar multi-type)”
High-speed with good planar accuracy
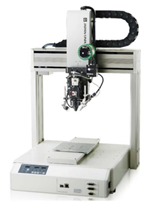
“Orthogonal desktop type (4-axis)”
No need for line configuration, easy to introduce
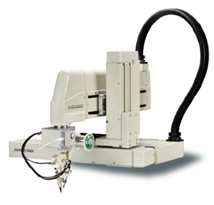
“Orthogonal type (4-axis in-line type)”
Good planar accuracy, ideal for flat boards
Demands for Future Soldering Robots
Currently, the manufacturing industry faces various challenges such as labor shortages, skill transfer, delayed IT utilization, and the transition to forms aligned with carbon neutrality and SDGs. Soldering robots are expected to address these challenges. When considering future soldering robots, the following four perspectives are particularly important:
Addressing Labor Shortages
s
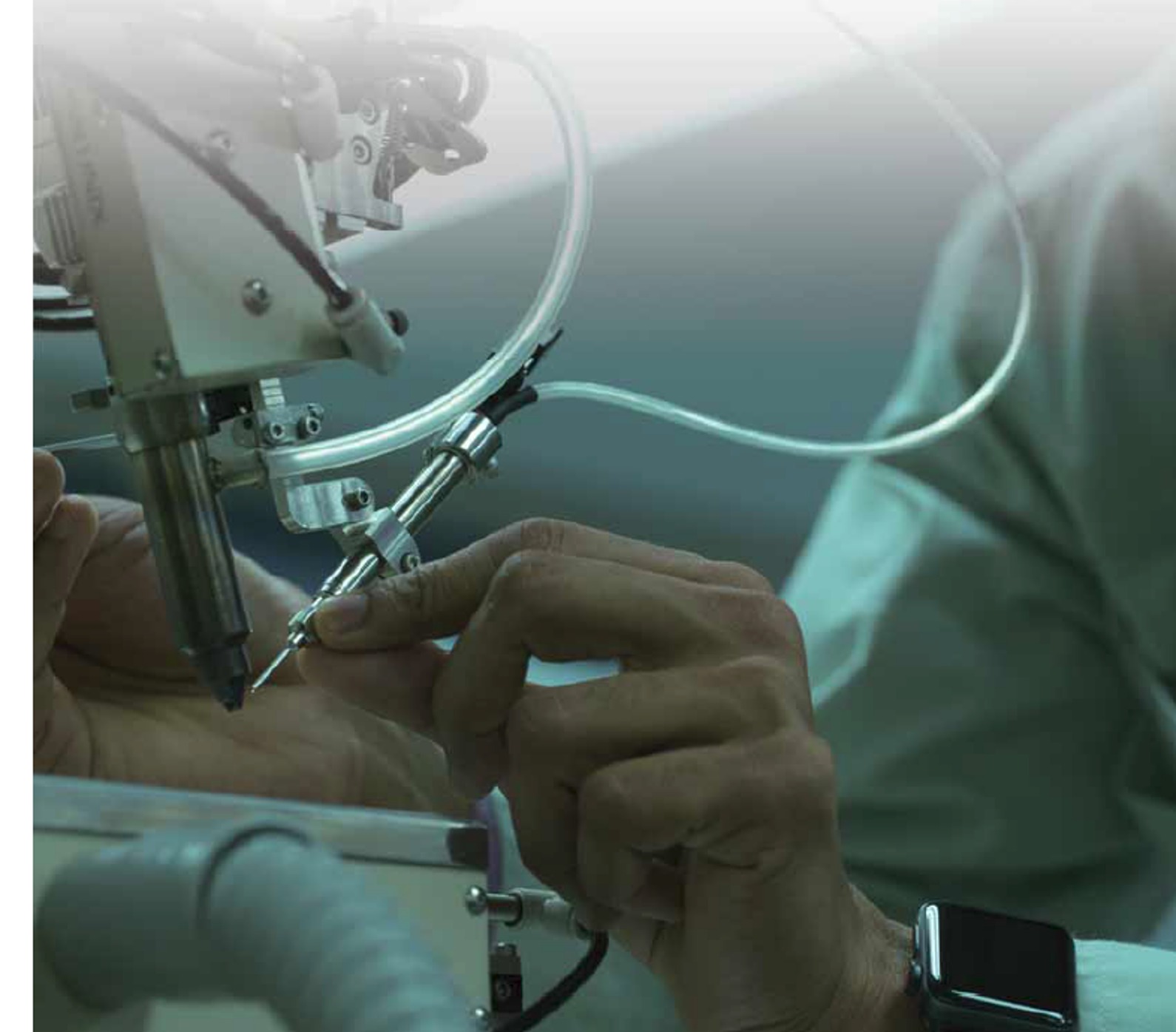
Further Visualization of Soldering Processes
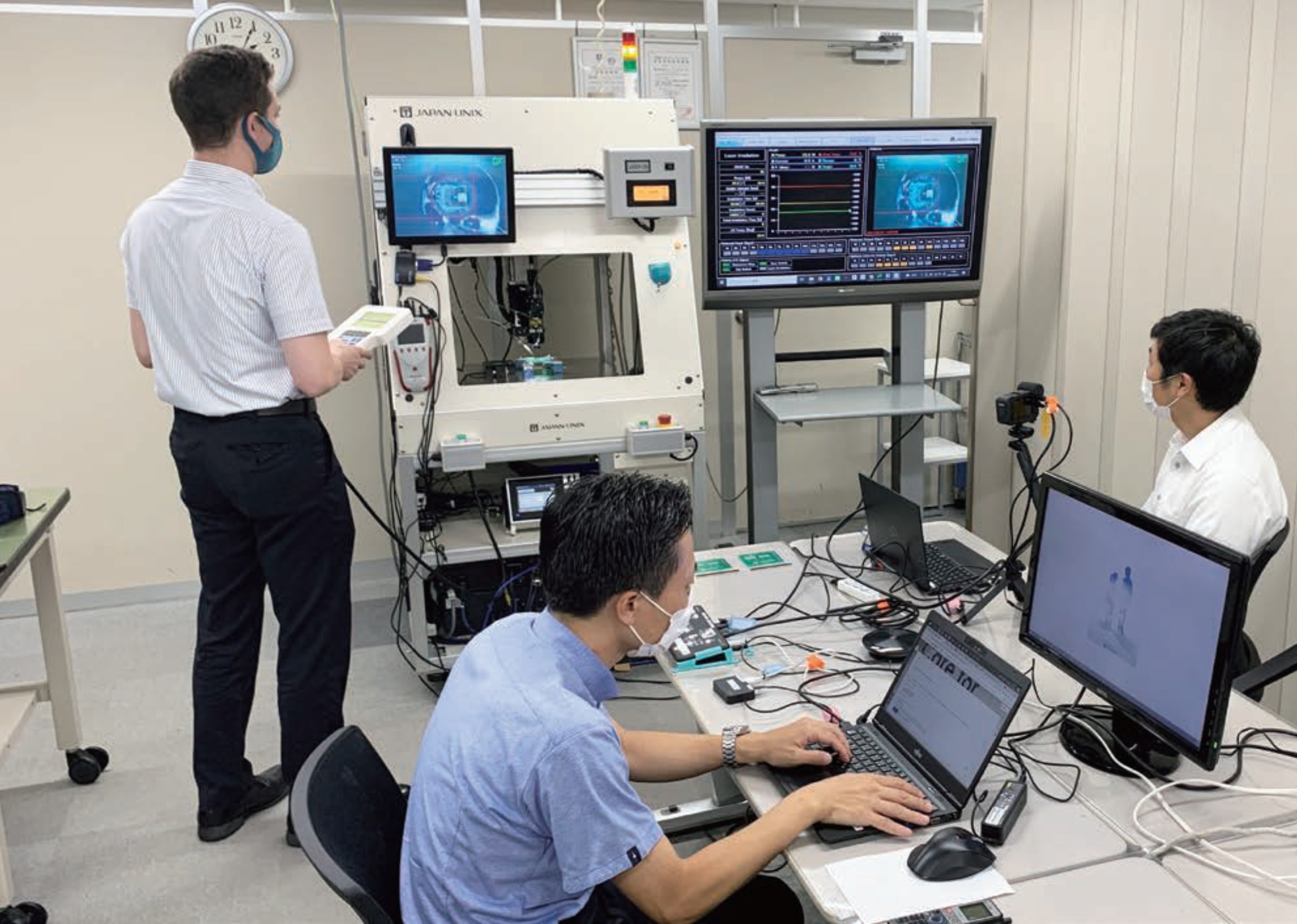
Adapting to High-Mix Low-Volume and Variable Production
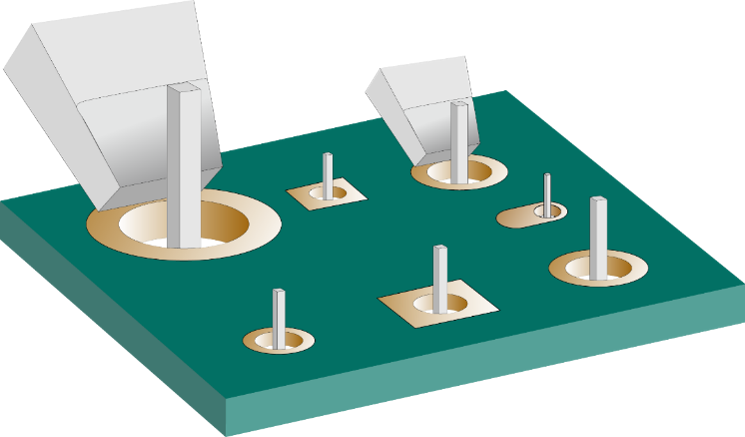
Approaching CO2 Reduction Goals
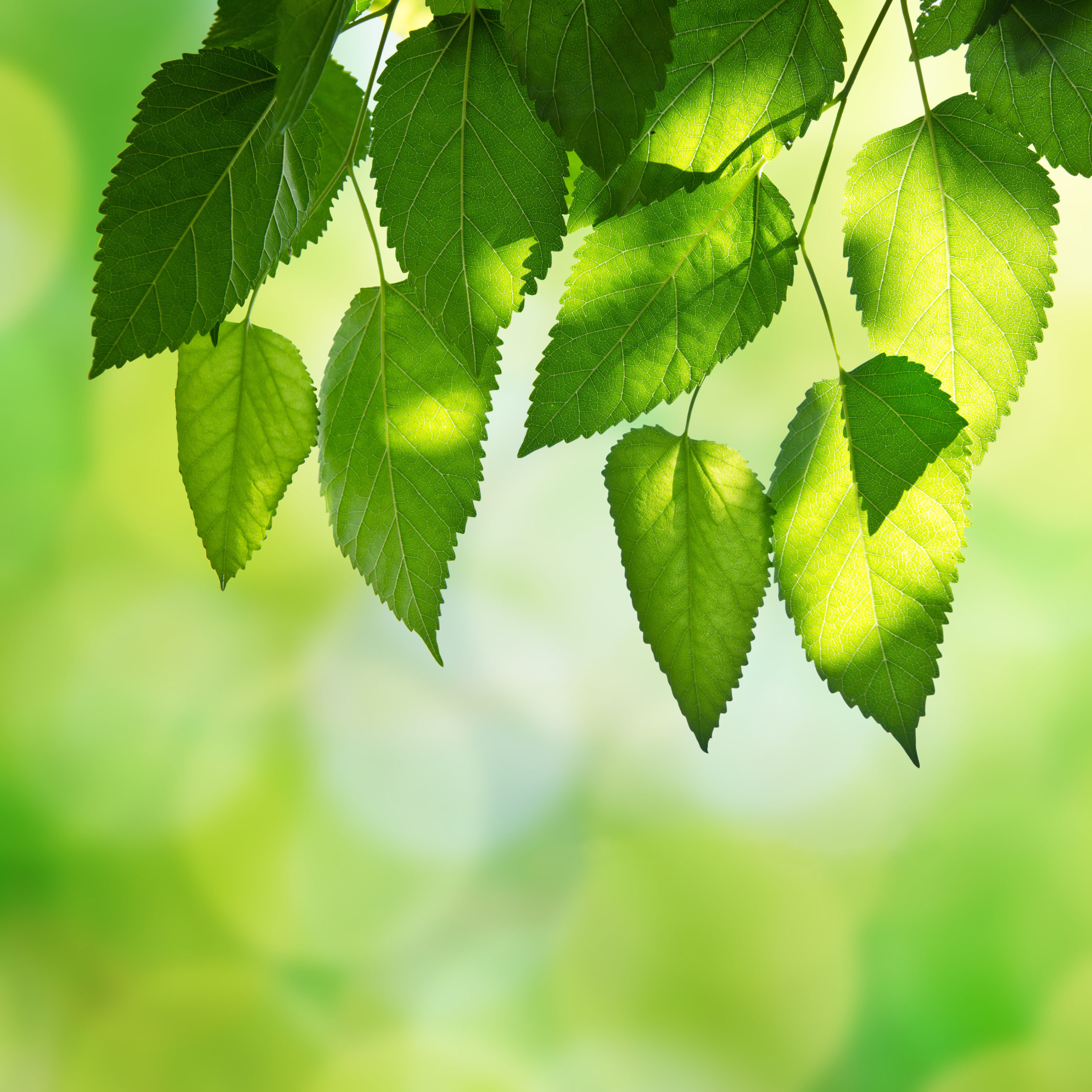
The Evolution of Soldering Robots Will Continue
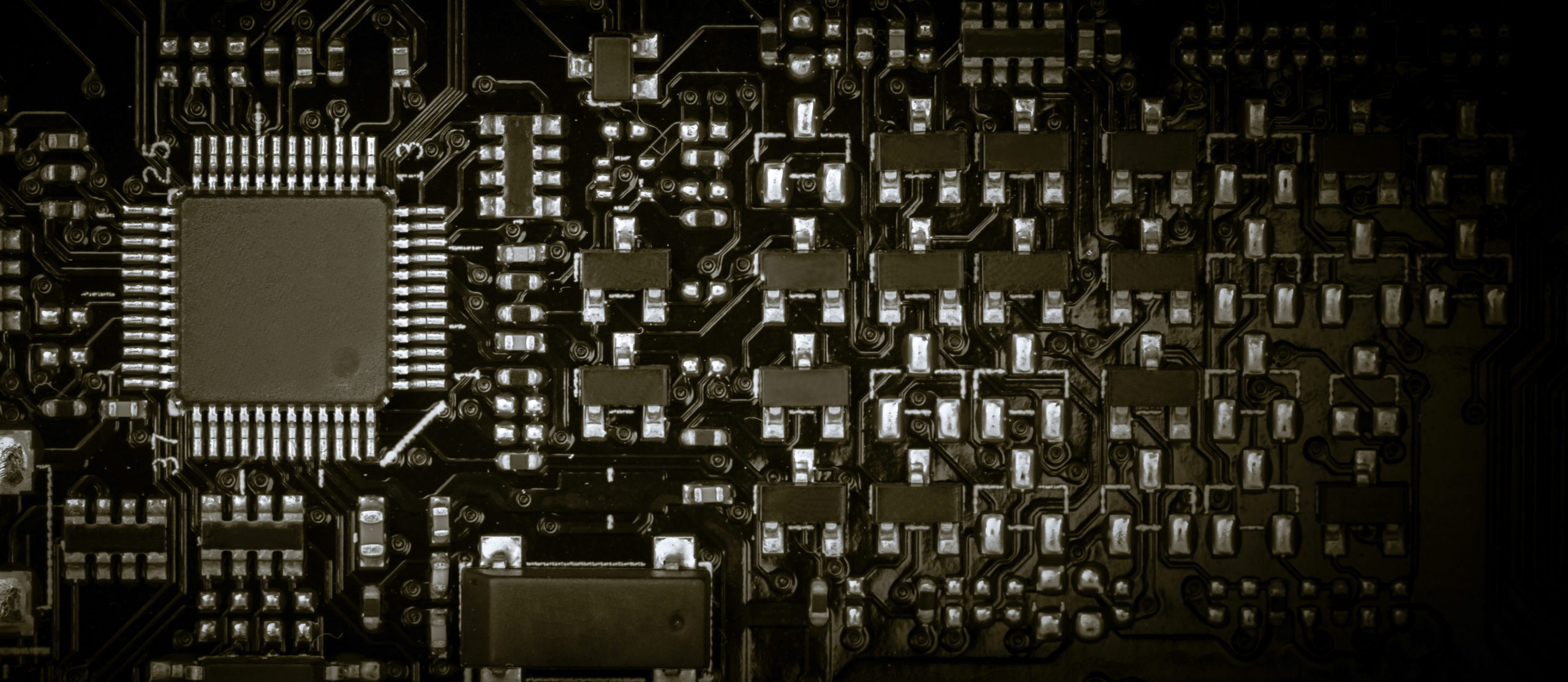